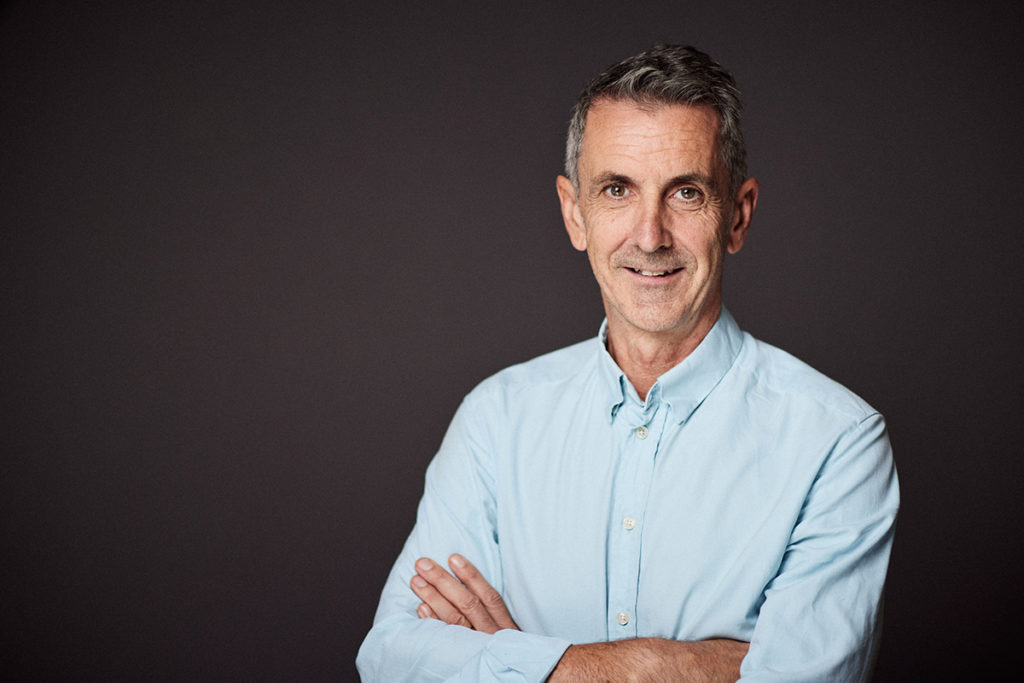
THE logistics and cost of obtaining information on packaging material could see firms opt to pay the recently introduced plastic packaging tax (PPT) without submitting evidence, a packaging expert has warned.
Andrew McCaffery, global EPR director at packaging data services provider Ecoveritas, told Packaging Scotland that the ‘complexity’ of the regulations means that businesses are struggling to get to grips with what information they are required to submit in order to comply.
“The way it’s written is really complicated,” he said, before warning that the ‘ambiguity’ of the writing has left the team at Ecoveritas having to reach out to have details clarified. “It’s a very complicated set of regulations; I don’t think companies understand what data and evidence is required; I think they think it’s going to be a straightforward process, but it’s proved to be anything but.”
The PPT is payable by UK businesses that manufacture or import ten tonnes or more of plastic packaging, which does not include at least 30% recycled plastic over 12 months.
Andrew believes the regulations were written with manufacturers in the UK in mind, as they would naturally have easy access to the information required. However, the fact that a significant amount of the plastic packaging which falls under the PPT is imported, means that companies will have to go directly to the foreign manufacturers to get the required information.
“The tax breaks it down into all of the components (of the plastic packaging),” Andrew said. “So, in the case of a bottle, the label and cap are both viewed as different items – so you have to get and submit the information on these if they are made from plastic.”
Warning that this could lead to a lack of compliance or companies simply paying the tax without submitting evidence to support recycled content, Andrew suggested that allowing companies to submit an average weight of, for example, bottles would be more cost and time-effective, as opposed to having to get the exact weight.
“I think there could potentially be a situation where people just say it’s easier to pay the tax than gather the evidence, because trying to obtain this information is going to cost more than the tax,” he added. “This would be the wrong message to put out, but if it’s going to cost you £10,000 to gather evidence to pay a tax that’s going to be £1,000, what would you do?”
Ecoveritas has developed a data collection vehicle (DCV), which helps businesses to map the data they have into the free tool.
The firm is also actively assisting companies to ready their submissions, as well as working alongside HMRC to showcase the methodology it is using to track the required information.
“We gather information on behalf of the companies,” Andrew added. “They give us their supplier information, we go out and gather the data, then prepare the templates for submission, and it makes life a lot easier for them.”
As of September 26, over 2,600 businesses had successfully submitted their Q1 returns on time. But with HMRC estimating that up to 20,000 businesses would be affected, Andrew warned that companies are at risk of, perhaps unintentionally, breaking the law and incurring penalties.
“HMRC are administering it, so it’s the same penalties as non-payment of tax,” he said, before stating there is a fixed fine of £500 for non-compliance and failure to register, followed by an additional £40 fine for each day of non-compliance.
“At the beginning, I think they’ll take a light approach for those being non-compliant,” Andrew explained. “But after a few years, I’d imagine there’ll be a different approach. It is a tax, so apart from civil there is a criminal potential as with any tax – it’s up to HMRC how they proceed with it.”
Believing that the lack of compliance is more down to genuine confusion than firms being rebellious, Andrew is calling for the regulations to be simplified. “I think they will have to make the information absolutely crystal,” he added. “For example, it needs to be clear that, even if all your plastic packaging contains above the 30% recycled content, you still have to register – that’s not a means of exempting yourself, despite what some may think.”
With an impending deposit return scheme set to join the PPT in attempting to support ambitious environmental aims, Andrew warned that additional pressure could be put on firms in ensuring their barcodes are registered to the Scottish system.
“Packaging is a very emotional subject and also very emotive,” he added, before explaining that it is containers not included in DRS, such as shampoo bottles, that drag down Scotland’s plastic bottle recycling rates. However, not much focus is put on this.
He explained that environmental goals usually ‘come in circles’, citing evidence from 2010 when there was a push to move from glass to plastic bottles in order to lower carbon footprints.
“You have to be careful you’re not just responding to a populous push, that you’re moving for the right environmental reasons. There’s more push than there ever has been on companies.”