Once medication is packaged, a wealth of regulations become applicable, including NICE guidelines and General Pharmaceutical Council standards of conduct. Here, Dale Pittock, sales director at pharmacy consumables provider Valley Northern, explains hassle-free ways of ensuring medication is kept safe throughout the entire pharmacy to patient journey
PACKAGING plays an important part in any product, but particularly in the pharmaceutical industry where it must not only convey essential information to the patient, but also protect the medication from external factors. Packaging however, can often be overlooked as an important part of pharmaceutical product development and prescription dispensing.
The World Health Organisation (WHO) guidelines on packaging for pharmaceutical products report states that “public opinion sometimes considers packaging to be superfluous”. The report continues by outlining that the complexity of packaging materials and the advanced nature of medical products means that manufactures are often confronted with problems.
The guidelines state that packaging must; protect against all adverse external influences that can alter the properties of the product (moisture, light, oxygen, temperature), protect against biological contamination, protect against physical damage and carry the correct information and identification of the product. As a result, selecting the right packaging for any medication is important.
Protecting medication
Ensuring that the packaging used for medication is fit for purpose is the first step in guaranteeing that the medication is protected from the external influences outlined in the WHO guidelines. Despite selecting the best packaging available, sometimes pharmacists are left to store items in less than ideal circumstances.
Opting for tablet cartons that are rigid enough to hold their shape when stored and medicine bottles that are designed to reduce the risk of contamination are simple and effective ways for pharmacists to comply to requirements. Traditionally, uncapped medicine bottles were the go-to style of bottle packaging for pharmacists. The bottles would be stored, often in unsterile places, and then selected and used for medication dispensing. However, this left significant risk for contamination. Now, pre-capped medicine bottles are considered industry standard, meaning the bottle is kept sterile and clean from manufacturing right through to dispensing use.
The reason packaging products like this can be at risk of contamination is that many pharmacists struggle to store the large quantity of packaging items that they order. By working with a supplier, like Valley Northern, that offers order storage options for customers that can’t house their entire supply, you are also kept safe in the knowledge that your paid for order isn’t going to be stored in an undesirable location before its required.
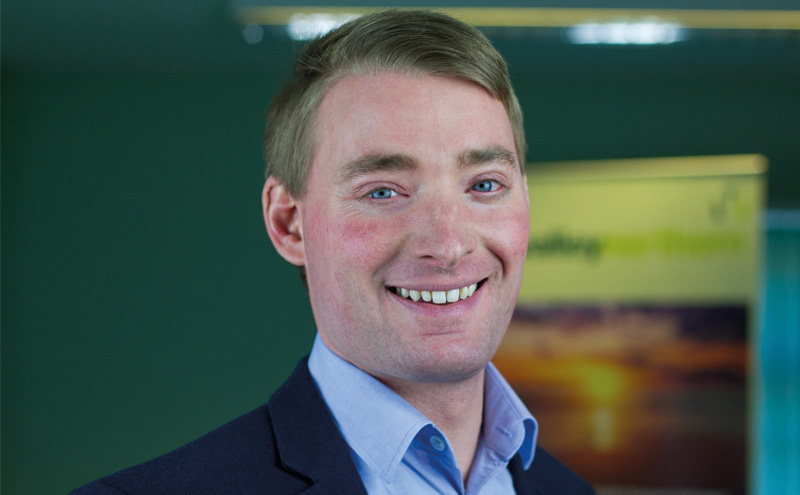
Protecting patients
In the UK, the Medicines and Healthcare products Regulatory Agency (MHRA) approves all packaging and labelling information for medicines and regulates the information that must be provided to patients. By law, the ingredients and dosing information must be available, but a leaflet in a plain white box is not the most reliable way to deliver vital information to patients
By selecting more distinct packaging, pharmacies can ensure that the medications they are dispensing to customers are distinguishable from other boxed items. Simple considerations, like printing the word ‘prescription’ on a carton, which may be an obvious inclusion, can help patients easily recognise what is prescribed and what isn’t. Creating bespoke packaging designs that include other distinguishable design elements, like the standard green pharmacy logo or your pharmacy’s brand colours, can further support patient safety. Valley Northern’s custom print service means that your customers can immediately recognise their medication and can support patient safety efforts.
Going the extra mile
Aside from the physical boxes and bottles of pharmacy packaging, supplying the right labelling and dosage aids can be the difference between a patient taking the correct dose or exceeding the prescribed amount.
Labels not only ensure that the right medication goes to the right patient, as patient information is printed and confirmed before dispensing, but it also helps pharmacists communicate essential information to the patient about storage or dosage. Eye catching labels, like the Status range of labels from Valley Northern, provide instructions for both the pharmacist and customer, like expiry dates, storage temperature guidelines or other vital warnings.
Despite best efforts, for some patients, packaging and labels don’t provide enough information to maintain safety. By offering patients disposable tablet trays that clearly define the time and day of the week that the patient should take the medication means that the chance of dosage errors is decreased and carers can closely monitor what medication has been taken and when.
Pharmacists have a duty of care to not only ensure their patients receive the right medicine, but also that the medicine they are dispensing is safe for use. Following the guidelines in place for the entire pharmacy and healthcare industry and implementing some simple but effective patient care initiatives, will help prevent accidental errors and regulation failures across the entire pharmacy, medication and patient lifecycle.