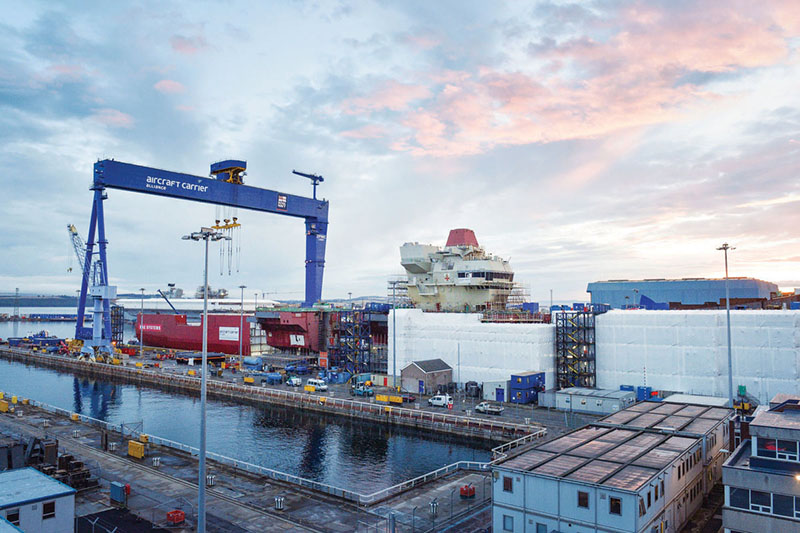
When you think of shrink wrapping you’re more likely to think of various types of food and clothing packaging than scaffolding and machine parts – but that’s exactly what Tufcoat specialises in.
Tufcoat provides transportation and weather protection and environmental containment through the use of shrink wrapping, primarily for the scaffolding, industrial and marine industries, and offers both installation and training for companies’ own staff to perform the operations themselves.
The company manufactures shrink wrap sheeting ranging in size from 7m x 15m to 14m x 50m.
“What we’re able to do with those incredibly large sheets of plastic is to cover objects, in instances, in single sheets, but the unique thing about our plastic is we can actually weld it together,” explained Tufcoat marketing manager, Barry Kirkham.
“Our installation teams use a propane heat torch, which allows them to bond two sheets together to create an even larger single sheet of polyethylene that will do any number of tasks and the same heat torch is then used to shrink off the plastic to create that drum-tight appearance around whatever object the shrink wrap is covering.”
Barry continued, “The benefits of shrink wrap are that it is a continuous sheet, whereas a traditional method of encapsulating a scaffold structure, for example, might leave holes or gaps in between lifts in the scaffold. Our sheeting will completely encapsulate or enclose an area so that has benefits from the weather protection side of things but also from stopping any dirt ingress as well, so you’ve got that kind of envelope, which contains and also protects from the outside, as well.”
The Plymouth-headquartered firm’s Scottish team is currently working with Wood Group Industrial Services on a project involving the Queen Elizabeth Class aircraft carriers in Rosyth where parts of the ship are being shrink wrapped in order to protect them while workers carry out painting and blasting operations.
Barry explained, “Throughout the last cycle of the ship construction different elements of the ship are transported from shipyards all over the country and once they arrive at Rosyth they are assembled to take the form of the main ship itself.
“What our shrink wrap does is enable them to both contain any pollutants from the blasting that they carry out but also to be able to protect the raw surface once that is prepared for painting to be able to allow the painting to cure at the correct temperatures.”
Barry added that the shrink wrap is suitable for “any industry that has an issue with the size of the product that they are looking to maintain, transport or renovate where a conventional material isn’t big enough or strong enough to withstand the applications that are being carried”.
He added, “The versatility of the product really is quite amazing depending on how our customers use it.”