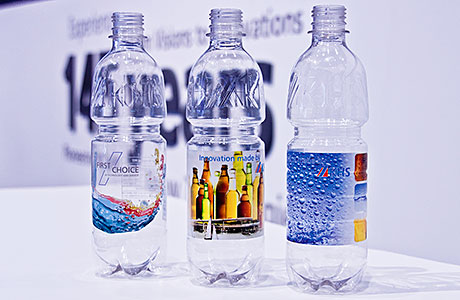
DORTMUND-based filling and packaging systems supplier KHS is among five companies nominated for the Hermes Award 2014 with its Innoprint direct print system for PET bottles.
The Hermes Award is offered every year in conjunction with the Hanover Messe, the world’s biggest industrial trade fair, and recognises innovative technology. This year’s shortlist also lauds developments in electric current sensors, electric power distribution and factory automation.
Matthias Niemeyer, CEO of KHS GmbH, said: “We’re very pleased, as direct printing is a milestone in the decoration of PET bottles.” Innoprint technology allows PET bottles to be directly printed all round. Compared to the plastic or paper labels commonly used to dress bottles to date, this process is said to be much more flexible. In addition, neither glue nor labels are now needed and these thus no longer have to be shipped or stored in air-conditioned warehouses.
Eco points scorer
Besides generating potential cost savings direct printing therefore also scores points for greater eco friendliness. And not just because the around 42 metric tons of labeling material and corresponding amount of glue used in the standard labeling process are now superfluous (at an assumed capacity of 25,000 labels per hour in two-shift operation on 220 days of the year); doing away with the logistics also cuts down on CO2 emissions.
Digital goes to press quickly
All the KHS Innoprint needs are text and graphics files, which it quickly prepares for printing. In theory, the machine is thus able to print each and every PET bottle with a different motif – at a rate of up to 36,000 bottles per hour. Digital printing considerably shortens time-to-market intervals. For example, at the end of a soccer game bottles could be printed with the result and a picture of the winning team and find themselves in retail stores in a very short space of time.
Suitable for food
The KHS Innoprint deploys inks suitable for food use. Their low viscosity and the use of intermediate UV curing also enable motifs to dry quickly and ensure that the ink adheres to the PET bottles. Recesses in or projections on the bottles can also be printed on. The print quality is excellent; an outstanding optical resolution of 1,080 x 1,080 dpi produces brilliant color images. The standard KHS Innoprint has five color carousels which apply white, cyan, magenta, yellow and black to the bottles in succession according to the CMYK color model. After printing very intense UV light reliably hardens the inks.
To help save resources and make the process sustainable PET bottles which have been directly printed on by the KHS Innoprint are suitable for bottle-to-bottle recycling. Here, the hardened inks can be completely removed from the shredded PET.
KHS believes the technology holds great potential and expects that direct printing will quickly penetrate the market. The company expects that within the next five years around 5% of all PET beverages the world over will be printed on instead of labelled.