The task of reducing our carbon footprint still has huge untapped potential but some firms are stepping up to the plate.
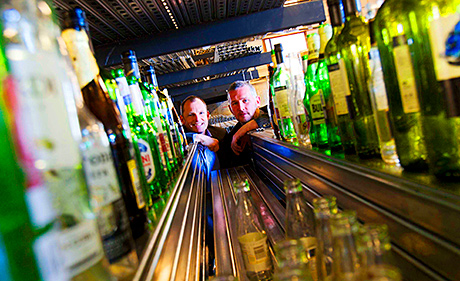
THE latest figures from the European Container Glass Federation (FEVE) estimate an average glass-recycling rate for the European Union of 68% in 2010, equating to some 25 million used bottles and jars.
Of these, 80% were remelted to make new glass containers in the ‘closed loop’ process which is unique to the glass industry and which produces new containers time and time again with no degradation in quality.
One firm that knows only too well the challenges facing the packaging industry is glassmaker O-I, which is a leading recycler of post-consumer glass containers, employing more than 24,000 people worldwide at 81 plants in 21 countries including its Scottish operation in Alloa.
Viivika Remmel, marketing director for O-I Europe says: “We are working with a host of stakeholders to increase the recycling of glass containers in all the countries in which we operate. We have ambitious targets to increase the amount we use in our production; every time we increase the recycled content of our glass, we enhance the environmental impact of our customers’ products.”
In addition to reducing landfill waste, recycling glass enables immediate energy and carbon emissions savings. Every 10% of recycled glass used in production results in a reduction in carbon emissions of approximately 5% and energy savings of about 3%.
Although 68% is a strong performance across the EU as a whole, O-I warns the UK industry in particular not to become complacent because at 61% the glass-recycling rate here is slightly behind the curve. As such, O-I’s UK business is particularly focused on working with local authorities both to increase volumes collected and to maximise closed loop recycling of glass into new bottles and jars rather than diverting the material to less environmentally valuable uses.
“We want to encourage people to keep on recycling and to consider whether any of their glass containers still slip through into general waste,” says Remmel. “Glass is a very easy material to recycle as it does not require extensive reprocessing before being returned to the furnace.”
Another business eager to bestow the advantages of glass and the circular economy is the engineering firm Tharsus. It has joined forces with the Scottish-based recycling experts Ekko Glass Crush and Collect to design and manufacture the glass compacting units for use in restaurants, bars, clubs and other licence trades.
Ekko has been piloting the unit with 100 customers that sell consumer glass in large quantities including Network Rail and FTSE 250 bar and restaurant chain Mitchells and Butlers.
Smaller than a wheelie bin the robust space saving units can reduce glass waste volume by 80% resulting in C02 savings for businesses.
Tharsus chief executive Brian Palmer said: “Working closely with the team at Ekko, we were asked to redesign the product to optimise throughout and satisfy international safety standards, while still meeting their commercial and technical specifications.”
Tharsus has completely changed the human interface point to make the product safer, removing the possibility of users coming into contact with glass shards and enhanced the ergonomics and aesthetics by adding a practical curved top to the machine.
Expected to be available by the end of the year, the new unit utilises the latest technology to make recycling more time and cost efficient, deconstructing all glass in one unit and, according to Palmer, reducing overall waste disposal costs for businesses by up to 40%.
Brian Williamson, director of Ekko, added: “One of the main hurdles to glass being recovered from the hospitality sector is the lack of storage space available at the properties.
“There is an increasing trend for ‘behind-the-bar’ in house compactors to be used to compact glass before collection which reduces the amount of space required to store the empty bottles and the frequency of collections required.
“After a successful pilot scheme with a number of companies, we needed a partner that could develop the design and deliver the product to a mass audience safely and after meeting with a number of different engineering and manufacturing companies, Tharsus stood out for us.
“We really liked what they had to say and we are looking forward to a successful relationship with them as they progress the development of the unit and then manufacture it on an ongoing basis.”
We were asked to redesign the product to optimise throughout and satisfy international safety standards.
The need for industry to focus its commercial and creative energies on ensuring their products meet the environmental credentials demanded by customers is acute in an increasingly ‘green’ society.
Innovative approaches to cutting waste are consistently highlighted by companies eager to prove they are leading the way and glass-packing specialist Beatson Clark is as good an example as any.
The company will be showcasing its new lightweight beer bottle at this year’s Food & Drink Expo at the Birmingham NEC. The 500ml tapered amber beer bottle can be manufactured in white flint and weighs just 285g – almost half the amount of its original beer bottle, which weighed in at 403g.
Marketing director Lynn Sidebottom said: “The bottle will be available from stock in the spring and will have a standard crown neck finish suitable for beers, ales or ciders, however it will also be interchangeable with an MCA finish to make it suitable for soft drinks.”
The benefits of lightweighting include reduced production costs and the ability to offer clients a more cost-effective product without compromising on quality. By reducing raw materials use and energy consumption, lightweight bottles can also help Beatson Clark meet waste reduction and emissions targets to fit in with the company’s green ethos.
The firm has also supplied a flexible and environmentally friendly solution for one of the country’s oldest soft drinks makers.
Purity Soft Drinks was established in 1892 and its Mason’s range of traditional carbonated drinks still comes in glass bottles delivered to the door.
Beatson Clark produced a bespoke returnable bottle for the range, which includes lemonade, dandelion and burdock and cream soda, amongst other traditional flavours. Purity turned to Beatson Clark for a new bottle when customer feedback showed a marked preference for traditional carbonates in glass bottles rather than the now more common plastic (PET).
Marketing manager Charlotte Taylor said: “The green credentials of glass as a packaging material are well known and Purity’s customers say the drinks taste better when supplied in a glass bottle. Our production flexibility also proved to be a great fit with Purity Soft Drinks, so we were happy to help.”
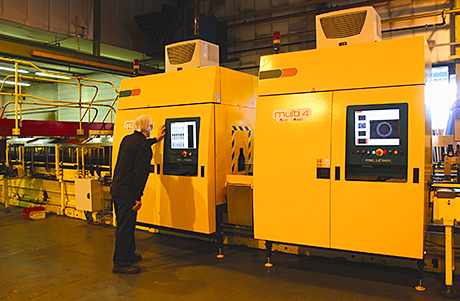
PURITY sales director Richard Perkins added: “Our returnable glass business has continued to grow despite the availability of inferior products in PET being promoted and heavily discounted by supermarkets. In short, we provide great quality, excellent value for money, a convenient delivered service and the added benefit that our packaging is reusable.”
Further developments at Beatson include an investment of £10m in furnace improvements and new high-tech equipment at its plant in Rotherham.
The firm, which celebrated its 260th anniversary last year, made a successful repair to its amber furnace in December 2011 and is planning a complete rebuild of its white flint furnace in July.
New automatic inspection equipment is also being installed which will further improve the quality of the products and improve traceability. The company has already installed new vision-based inspection equipment with sidewall, base and top stress detection on four lines, and installation on the other four lines will be complete by early next year.
Beatson Clark is also replacing M machines on all lines with the latest Servo-driven multi-inspection machine which inspects the neck of the bottle, wall thickness and ovality of the glass.
All this new equipment can read dot coding, which will enable additional automated inspection and improve traceability of the product. The company plans to add dot coding to all its products to take advantage of this facility.
Beatson Clark will also be upgrading its metal detectors across all lines later this year. As well as detecting metal in the product the new equipment will also isolate affected products and remove them from the waste products that go for recycling.
Managing Director Tony McLoughlin said: “We are always thinking about how we can improve our products and processes and constantly looking for new ways to provide an even better and more flexible service to our customers.
“The fact that we are making such a significant investment in our plant in South Yorkshire is great news for the region and an indication that we see growth in the food, beverage and pharmaceutical sectors over the next 12 to 18 months.”
As well as improving the production process, Beatson Clark is also investing in new design technology. The company has updated its CAD (Computer-Aided Design) system to the latest 3D visualisation software.
“Using this software during the new product development process, our design team will be able to provide customers with real-time images of what the end product will actually look like,” said McLoughlin.
“The animation of the 3D visualisation can be turned 360° on the screen, showing customers what the size, shape, colour and embossing details would actually look like, rather than using an outline drawing that takes time to amend and makes it difficult for customers to properly visualise the product.”