AN innovative materials company first launched from a Fife kitchen is nearing the opening of its first ever commercial production facility in America as it ramps up efforts to replace plastic packaging with fibre-based barrier alternatives.
Dalgety Bay-headquartered CelluComp will open the 15,000 sq. ft facility in Renville, Minnesota, in May, where it will then begin producing the firm’s micro-fibrillated cellulose product, Curran.
Curran is created by extracting cellulose from the residual pulp of root vegetables, with the resulting product able to be applied to the substrate of packaging as well as a coating on that substrate to improve the barrier properties and ultimately mean that products such as fibre-based bottles don’t need a plastic liner.
The company partnered with California/Singapore-headquartered RyPax to create an all-fibre bottle, and utilises Curran alongside bamboo and bagasse to create a material with ‘minimal’ porosity – meaning a thin impermeable coating can be applied to the inside, rather than a plastic liner.
Other applications include moulded fibre trays and plates, formable paperboard, and paper packaging with barrier properties.
“The idea in packaging is that you put the Curran material in the substrate,” Christian Kemp-Giffin, CEO of the CelluComp, told Packaging Scotland. “So, in a tray, it closes the porosity of the paper, smoothes the finish, and strengthens the tray. You then apply a very thin layer of the coating as you don’t want to have the tray porous – because paper is naturally porous – because if it’s porous and then you put the coating on, it’s all going to go into the tray, as opposed to lying on the tray.
“If you close the porosity of the paper and then put a drop of the coating on, it hardens and dries before it sinks in and then it’s also much more recyclable.”
Originally used as an alternative to carbon-fibre, Curran replaced 30% of the material in CelluComp’s creation of an award-winning fly fishing rod – halving its weight and making it the lightest rod of its kind at the time. Around two tonnes of the material is produced as an additive for paint, with it proving to be a valuable tool in the prevention of cracks during the drying process in warmer countries.
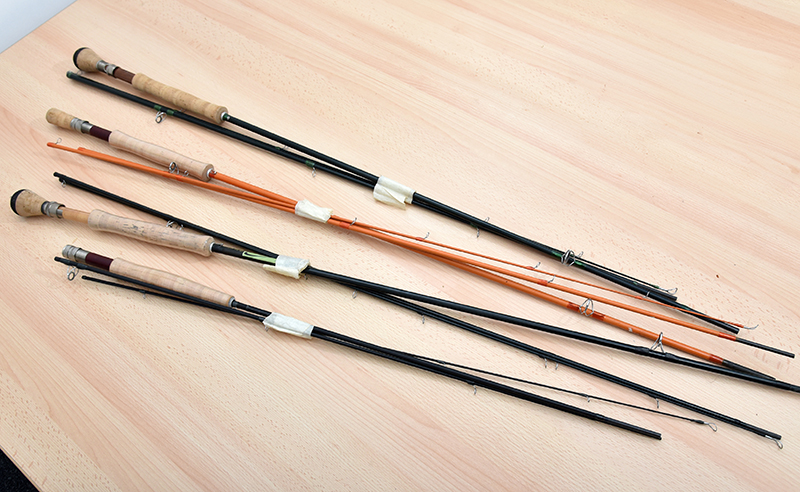
It wasn’t until 2018 when the company pivoted to developing Curran for fibre-based barrier packaging, amidst rising demand for sustainable alternatives, partly due to the release of David Attenborough’s widely acclaimed Blue Planet II which shone a light on marine plastic pollution.
“If the market isn’t ready to adopt it, then you’re doing what we call a technology push,” Christian replied when asked why the business didn’t start out in packaging. “You’re trying to force people to take something they don’t want – even if you’re telling them it’s good value for them, they’re not accepting it yet.”
Hailing the support of the Scottish Government and Scottish Enterprise, Christian revealed that Minnesota has also been ‘incredibly supportive’ with the University of Minnesota, the city of Renville, members of congress, the Minnesota Department of Employment and Economic Development, and local farmers all throwing their weight behind the work.
The state proved to be the ideal location for CelluComp’s first commercial factory, not least because of the 11 million tonnes of sugar beets grown there each year, with the United States Department of Agriculture deeming it to be the country’s leading sugar beet grower.
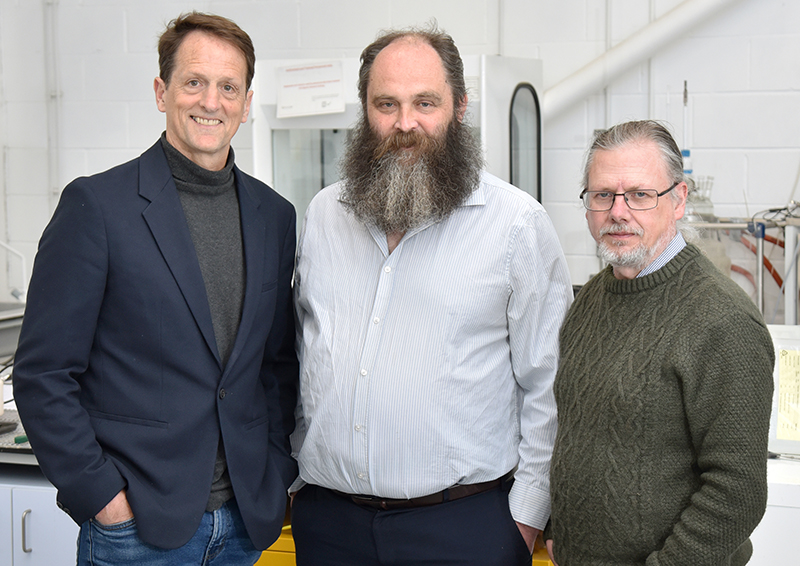
Supply levels are critical to CelluComp’s Curran operations. Curran translates to ‘carrot’ in Scottish Gaelic, which was the original vegetable pulp of choice chosen by founders Dr David Hepworth and Dr Eric Whale.
However, even in the early days, stock levels proved difficult to acquire – leading to the pivot to sugar beet pulp, a byproduct of sugar production, which proved to be a more viable alternative due to the scale of the global sugar industry.
The Southern Minnesota Beet Sugar Cooperative has already pledged to supply CelluComp with up to 7,000 tonnes of sugar beet pulp to produce 800 tonnes of Curran in the factory’s first year, before scaling it up to 24,000 tonnes in 2026. In total, CelluComp anticipates preventing 80,000 tonnes of sugar beet waste each year.
Once in production, CelluComp will look to tap into Chicago’s food market, with the Windy City home to the HQ of the likes of Kraft Heinz, McDonald’s, Ingredion, GrubHub, and ConAgra Brands. Plans are also afoot to expand into other countries too.
“Our plan has always been to roll out multiples of these factories producing the Curran material and those would be in geographical markets,” Dr David Hepworth added. “It just so happens that the US has been the first – we plan on doing something else in Europe and then maybe the Middle East and Asia, and might even use sources other than sugar beet pulp to feed those factories.”
Plans are also in place to ramp up operations in Scotland, although not to the level of America due to the UK producing fewer sugar beets, with the Dalgety Bay R&D hub set to focus efforts on creating circular secondary packaging – such as options for the food and beverage industry.
“There’s a lot of other waste streams that get ignored due to the product not being good, strong, or valuable enough to make secondary or primary packaging, but when you mix Curran with it, then it levels up and allows it to suddenly become viable,” Christian explained, before Dr Hepworth revealed that a project is hoped to start shortly which will target certain waste streams in the UK which, in turn, will increase business at the Scottish base.
“We do have a separate business plan for Scotland,” Dr Hepworth continued. “This (Dalgety Bay) has automatically become the R&D centre, but we want to go beyond that by developing some business which can be circular business specifically in Scotland – so relatively soon that might involve separate manufacturing capabilities, which we may need to increase here in Scotland to be able to serve some of these projects where we’re valorising the waste streams and potentially selling to customers in Scotland.”