By Ben Elkington, innovation director, food packaging, kp (Klöckner Pentaplast)
THE meat and protein industry is about to experience a seismic overhaul of the packaging regulations under which it operates. The European Union’s Packaging and Packaging Waste Regulation (PPWR) is due to enter force at the end of 2024 – and as it does, recyclable packaging goes from ‘nice-to-have’ to a regulatory requirement and business imperative.
While the final details are still being ironed out, it’s clear that this regulation will fundamentally reshape how we approach packaging design, material selection, and end-of-life considerations for meat and protein products. But is the industry ready for this shift, and what steps can brands and their packers take to ensure compliance whilst maintaining product quality and safety?
The aim of PPWR
The ultimate goal of PPWR is to reduce the amount of packaging waste sent to landfill across the EU. To achieve this, the regulations will phase in a wide-ranging package of measures, harmonised across every member state. This includes packaging reduction targets, recycling targets (both incrementally increased every five years), recycled content targets, and harmonised design for recycling (DfR) guidelines.
For meat and protein producers, and particularly those that aren’t yet using recyclable packaging, this means rethinking packaging strategies from the ground up. One of the central aspects of PPWR is that all packaging should be recyclable by 2030. This involves meeting specific criteria as to what qualifies as ‘recyclable’, including compatibility with industrial-scale collection, sorting, and recycling processes.
Additionally, PPWR mandates minimum levels of recycled content in plastic packaging, with percentages set to increase over time. This poses particular challenges for food-contact materials, where safety and regulatory compliance are essential. And for meat and protein businesses, these challenges are even more pronounced.
A unique challenge for the meat industry
Maintaining food safety, extending shelf-life, and preserving product quality are paramount concerns that can sometimes, seemingly, conflict with sustainability goals. Traditional packaging solutions like multi-layer laminate films or absorbent pads, whilst effective, often hinder or complicate recyclability.
For instance, many current meat packaging solutions rely on multi-layer structures combining materials like polyethylene (PE), polyethylene terephthalate (PET), and ethylene vinyl alcohol (EVOH) to provide strong barrier properties.
While effective, these multi-material structures are notoriously difficult to recycle in standard waste streams. Similarly, absorbent pads, typically made from a combination of plastic and cellulose materials, can contaminate recycling streams if not properly separated. The good news is that packaging innovation is accelerating at pace to meet these challenges.
Achieving the balancing act
Meeting the PPWR’s ambitious targets will require high-level cooperation across the value chain. Meat and protein producers need to work closely with packaging suppliers to co-develop solutions that meet functional, packaging efficiency and sustainability requirements, without making compromises.
What’s more, collaboration with recyclers is essential to ensure new packaging designs are truly recyclable in practice, not just in theory. At kp, we actively engage with recyclers and waste management companies to understand the practical challenges of recycling different packaging materials.
This collaboration informs our design process, ensuring that our innovations are not just theoretically recyclable, but practically recyclable in real-world conditions. We’ve been manufacturing high-quality fully recyclable PET products for years and we are constantly transitioning our portfolio to ensure all our products are recyclable.
As an example, our kp FlexiFlow EH 155 R and kp FlexiFlow PH 255 R barrier flow wrap films are both fully recyclable. kp FlexiFlow PH 255 R, a polypropylene-based (PP) film, contains more than 93% PP, exceeding current packaging guideline specifications for recyclability.
Its polyethylene (PE) counterpart, kp FlexiFlow EH 155 R, raises the bar even higher with over 95% PE content, breaking new ground for recyclable barrier films.
Even though it is clear great progress has already been made by the industry, the transition to fully recyclable meat and protein packaging won’t happen overnight.
It requires a fundamental rethinking of how we protect, preserve, and present our products. However, brands that embrace this challenge proactively will be ideally positioned to thrive in a post-PPWR world. At kp, we’re committed to partnering with meat and protein brands and packers to navigate these changes. We believe PPWR represents both a challenge and an opportunity for our industry. By working together and embracing innovation, we can create a more circular future for meat and protein packaging – one that benefits businesses, consumers, and the environment alike.
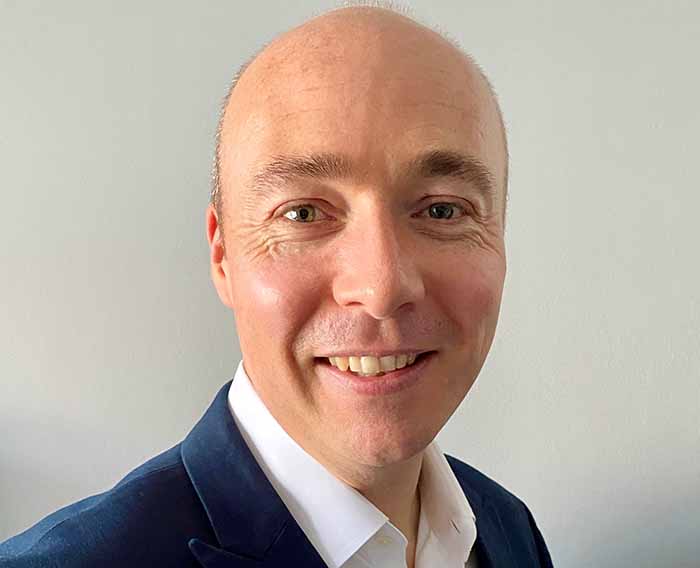