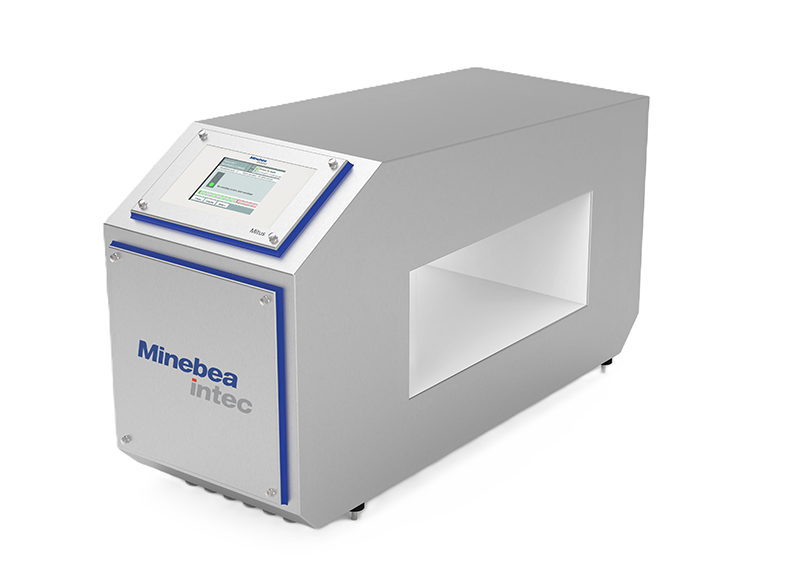
PROMOTIONAL FEATURE
The requirements for hygiene and product quality in the food industry are very high due to strict international regulations such as HACCP, ISO 22000 and NSF. Food manufacturers are required to use reliable and highly accurate technologies to meet these food standards. At the same time, they need to implement efficient solutions to reduce their costs and secure their margins in the face of rising raw material, energy and labour costs.
As a leading global provider of weighing and inspection technologies, Minebea Intec offers customised solutions that are precisely tailored to meet the challenges of food production.
Food control through HACCP (Hazard Analysis and Critical Control Points)
The HACCP system, which is used in the food industry worldwide, is a preventive management system for ensuring food safety. It requires producers to identify and assess potential hazards (biological, chemical, physical) throughout the entire food production process. Based on this analysis, critical control points (CCPs) must be defined at which risks are eliminated or minimised by preventive measures. HACCP is considered a mandatory requirement for food production in the European Union and in many other countries worldwide.
Minebea Intec technologies, such as the Mitus® metal detector, are ideally suited for monitoring and controlling such critical points. “Our Mitus® metal detector with integrated MiWave technology offers an effective solution for foreign body detection,” says Linus Dellweg, Global Product Manager at Minebea Intec. “With its high sensitivity, the Mitus® metal detector can detect even the smallest metal particles, even with larger product effects, and thus makes a decisive contribution to ensuring that food products meet the highest safety and quality standards.” The result: maximum product safety at maximum output.
In addition to metal contaminant detection, Minebea Intec offers solutions with its X-ray inspection systems that detect not only metallic foreign bodies but also glass, stones, plastics and bones. Systems like the Dymond series go far beyond mere food inspection for foreign bodies: they check the integrity of packaging, control fill levels and detect product damage. With these comprehensive functions, X-ray inspection systems make a significant contribution to compliance with international hygiene standards and to product safety.
Food standard ISO 22000
The international standard ISO 22000 defines uniform requirements worldwide for management systems for food safety. It covers all stages of food production and aims to ensure consistent food safety, from production to delivery.
The precise and reliable weighing and inspection systems of Minebea Intec help food producers to meet the requirements of ISO 22000. These include dynamic checkweighers, which monitor product weight in real time during the production process. They ensure that products have the correct weight and immediately detect deviations.
Scales also promote traceability by collecting important data such as weight, time stamp and batch information that can be used for documentation and analysis. In the event of quality issues, the data collected enables quick identification and traceability of affected products.
With the introduction of the new Blue HMI for checkweighers, Minebea Intec is setting a new standard in user-friendliness and efficiency. This advanced user interface offers numerous smart features to optimise production processes.
Whether you need to teach in a new product, adjust line parameters or define a batch protocol, The new Blue HMI user interface makes working with checkweighers easier and more efficient.
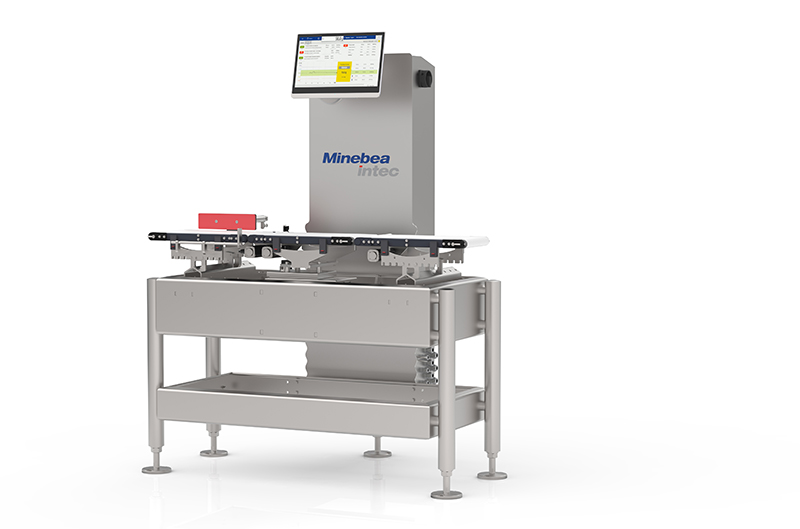
“The design concept of Blue HMI is based on what we are familiar with from our daily use of high-tech devices. The user-friendly menu navigation and new workflows make it much easier to use and reduce the training period,” says Lars-Henrik Bierwirth, Global Product Manager at Minebea Intec.
Since checkweighers are often located at the end of a production line – which is also a critical control point – the integrated overall equipment effectiveness provides a clear overview of the efficiency of the production line as a whole. There are also special combination checkweighers that integrate a metal detector into the smallest of spaces and additionally check products for possible contamination.
The new Blue HMI offers Minebea Intec customers even more potential for automation and process optimisation through a variety of interfaces, including traceability.
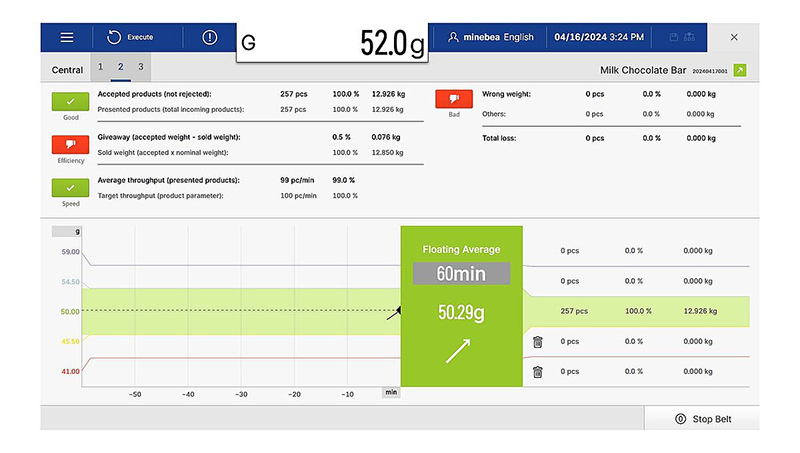