By Sam Tilley, regional general manager (UK, Ireland & Nordics), OMRON
Whether working in automotive or logistics, fast-moving consumer goods (FMCG) or food and drink, some factory managers can take an ‘if it ain’t broke, don’t fix it’ view. This approach is understandable, particularly if it relates to a process that took a long time to get right in the first place, or a line or machine that is running reliably.
However, reducing Scope 1 greenhouse gas (GHG) emissions in the order of magnitude necessary to meet 2050 targets will entail the modification of many existing plants and processes – even those that are working perfectly.
Luckily, we do not need to start from scratch to achieve our goals. Intelligent energy management, or the optimisation of energy use within an organisation, can help identify potential areas of improvement, and guide the adoption of practical, feasible ways to decarbonise operations.
Materials handling and GHG emissions
A single forklift generates around 2,640 grams of carbon dioxide (CO2) per litre of diesel combusted, resulting in between 5,280 and 7,920 grams of CO2 emissions an hour. Opting for more sustainable methods of on-site materials handling, then, could represent a significant GHG saving.
Autonomous mobile robots (AMRs) are battery powered, making them the perfect fossil-free alternative for transporting boxes and pallets. They are also intelligent enough to return to the charging station when they need to, optimising workflows even further.
They also represent a dynamic replacement for conventional linear conveyors. What’s more, unlike traditional autonomously guided vehicles (AGVs), they require no facility modifications, such as floor magnets or navigational beacons, making them relatively simple to adopt.
Robotics can also drive greater energy efficiency in palletising, where the rise of e-commerce and the trend towards high mix low volume (HMLV) manufacturing has made mixed pallets more common.
With fewer pallets equalling lower per unit carbon emissions, optimising the various patterns to make better use of space in transit and storage requires complex programming. Collaborative robot (cobot) palletising solutions, work alongside human workers to quickly calculate pallet pattern definitions, and significantly reducing programming time and making it easy for operators to implement changes.
Reducing wasted energy
There is no getting away from the fact that factories require vast amounts of electricity. Everything that moves, whether it’s a motor, pump, drive, or fan is driven by energy, and organisations need to think about what they can do to reduce waste.
In the average industrial facility, between 10 and 30% energy consumption is used to generate compressed air. Yet up to a third of that air is often wasted, due to leaks, misuse, over pressurisation, and pressure drop. Using smaller compressors for reduced needs, installing electronic speed variators and heat recovery systems, and limiting pressure loss can all make compressors more energy efficient.
With pumps, optimising flow control and motor performance, ensuring they meet efficiency class IE4 requirements, will help increase energy efficiency.
The importance of inverters shouldn’t be overlooked. Inverter technology has advanced considerably in recent years, and while those made 20 years ago might still work, they won’t incorporate regenerative energy capabilities. Replacing old inverters, then, could make a huge difference to the energy efficiency of equipment.
Data-driven change
The reductions in energy usage needed to achieve ambitious net zero targets, however, can rarely be achieved on the factory floor alone. Smart use strategies that harness the internet of things (IoT) and artificial intelligence (AI) models can help factories analyse their real-time production line data usage data, to identify efficiencies. This helps manufacturers to implement solutions, which may be as adjusting the settings on inverters.
To collect this data, facilities will need sensors, something that old lines may not have, at least not in the correct locations or with the required accuracy. While sensorisation is a pre-requisite of any smart monitoring data management platform, it can be a very worthwhile investment, providing manufacturers with insights they may otherwise have remained hidden.
When such a system was used to continuously monitor the air and operational situations in a factory clean room, for example, it found hours in which production and quality were unaffected when the air conditioning was turned off. It meant the team was able to implement a new policy on air conditioning use, significantly reducing energy consumption and the related costs.
Adapting to a sustainable future
While there are some areas of manufacturing where small adaptations can lead to big savings, reaching net zero will also require fundamental changes in areas such as the collection and analysis of production data, and the movement of goods around the factory floor.
Innovative new technologies will play a role but it’s a myth that manufacturing facilities have to be new to be energy efficient. There is plenty that can be done to make existing factories and production lines more sustainable.
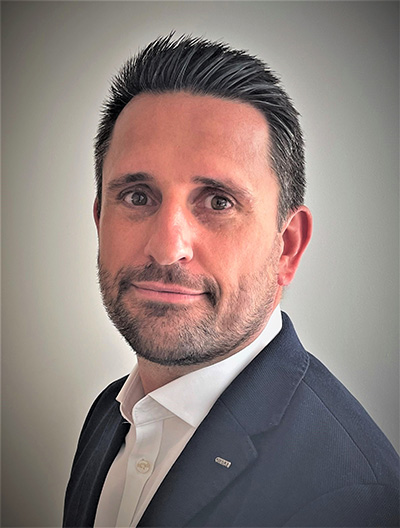