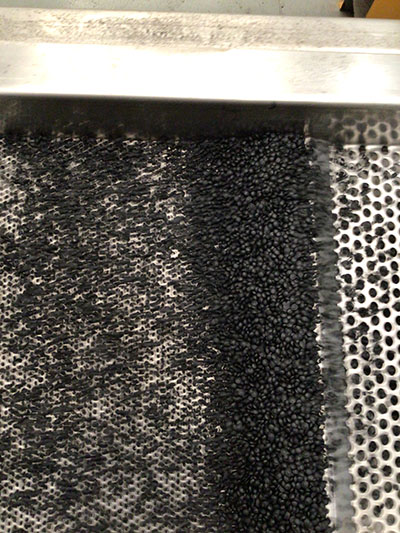
James Cropper, pioneer of what has been described as the world’s first technology to ‘upcycle’ used coffee cups, has revealed it can now recycle both the waste plastic and the paper from each disposable cup.
Until now, the firm explained that 5% of waste plastic removed from each cup was being used as a source for energy recovery in the production of recycled paper. However, working with partners Cumbria Waste and New Horizon Plastics, recycling the waste plastic into new plastic products has been made possible, giving the entire cup a second life.
The plastic is made into pellets and then used, most likely, in commercial packaging and agricultural applications. Meanwhile, the paper fibre from the cup is made into new paper products and premium packaging.
Rob Tilsley, fibre operations group leader from James Cropper, said, “Recognising value in the high quality fibre used to create paper cups, we were inspired to convert this enormous waste stream into a value stream instead, and now we’ve taken it even further. Working with our local waste management partner, Cumbria Waste, we have been relentlessly exploring sustainable opportunities where the cup plastic can be recycled or reused locally.
“Following extensive trials, New Horizon tested and approved the plastic waste, which is separated from cups during the CupCycling process, and it is now collected by Cumbria Waste and recycled by them in North Wales.
“New Horizon Plastics, one of the best plastic reprocessing companies in the UK, has the capability to shred, wash and turn the cup’s waste plastic into pellet form. Processing around 155 tonnes of plastic every day, the clean plastic pellets eventually end up in a range of products such as bags and wraps to plastic gates, animal pens and grain stores.”
The latest CupCycling development comes as the paper mill bolsters its sustainable credentials. James Cropper has commissioned new commercial packaging designed to protect paper from moisture ingress during transport, with 30% recycled content. The company added that the new wrap has a high stretch percentage which has also enabled the papermaker to reduce the amount of protective plastic packaging it uses by a third.