THERMOFORMED packaging specialist Macpac is celebrating 50 years in business this year.
The company described half a century of conceiving, designing, and manufacturing packaging as ‘no small feat’, particularly when taking into consideration how it has had to evolve to meet increasing demands around environmental concerns.
Macpac explained that the milestone is the result of the combined efforts and hard work of every individual within the business and is ‘more remarkable’ for a privately-owned manufacturer to survive and thrive within a packaging sector that is ‘notorious’ for its short-stay players, where there are numerous acquisitions, takeovers and mergers.
The family-run business revealed it has ‘consistently delivered excellent customer service’ and provided packaging in a ‘timely and cost-effective’ manner during a time that has seen a tumultuous evolution in packaging design and advances in materials technology.
Testimony to this success is the number of customers that have remained loyal to the company over several decades.
The early days….
In 1973 the company was founded by Chris Kershaw, father of the current owner and MD, Graham Kershaw. The firm was born out of the demand to produce packaging for Dinky Toys and Meccano and operated on the first floor of an old printing mill. With the invention of thermoforming, growth was described as ‘rapid’ and in the 1970s the business re-located to Macclesfield, out of which the name Macpac was born.
Expansion….
The business continued to expand throughout the 1980s, with a further move to Bredbury in Stockport due to outgrowing the Macclesfield site. In 1990 Macpac gained ISO9001 accreditation for development processes put in place for tooling development.
A low point in the company’s history came in 1996 when a devastating fire at the Bredbury factory prompted the move to the current address on the Heaton Mersey Industrial Estate in Stockport. Occupying just a single industrial unit with a modest four thermoforming machines on site, Macpac revealed that the business continued to operate and grow.
Keeping it in the family….
In 1997 Chris Kershaw’s son, Graham, returned to the business after graduating from university and working overseas for 10 years on robot control systems. It is this interest in manufacturing processes and commitment to the environment that would be a guiding factor in the direction Macpac would follow in the years ahead, influencing the ‘green’ credentials of the company’s packaging designs and choice of materials.
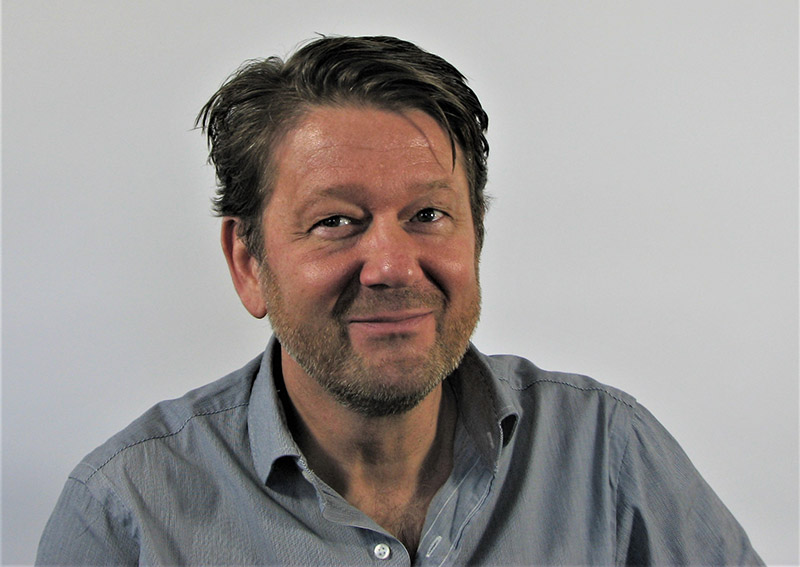
By 1998 Macpac realised that to achieve increased productivity it had to modernise its processes and introduced Computerised Numerical Control machines (CNCs) into its toolroom. Macpac explained the departure from traditional cast aluminium toolmaking provided ‘highly accurate’ CAD/CAM machining and gave a competitive edge whilst speeding up the process. Over the following years the company would continue to invest in supporting the tooling manufacture process, which in turn plays an important part in feeding the thermoforming machines.
The next generation….
In 2000 Chris Kershaw decided to take a step back from the business and Graham became the new MD. This was described as a turning point in Macpac’s history – with an injection of new investment and ideas to grow what was already a well-established business, into the force it has become today.
RPET takes centre stage….
In 2003, there was a stampede to move from PVC due to recycling issues and heightened concerns for the environment. Macpac was to be a forerunner in the application of its preferred replacement – Recycled PET (R-PET) – promoting the uptake and use of the material across a range of markets. In 2005 Macpac entered the medical/pharmaceutical sector, using R-PET as the choice of material in its design of the first thermoformed dosage pill tray, which was to revolutionise the administration of tablets to patients. R-PET has now become the most widely used of all thermoforming materials and by 2023 makes up over 90% of the material Macpac processes through its factory.
The scalable process
By 2008 and following investment in new thermoforming equipment, Macpac had doubled the size of its factory with the acquisition of adjoining units, with later expansions to the site for larger raw materials and finished goods warehousing. In 2010 and a further investment in new machinery and staff, the company achieved BRC/IOP accreditation which it has retained ever since.
2011 saw Macpac acquire Hamilton Packaging, which expanded the firm’s customer portfolio and introduced Macpac to new markets.
Working with German machine manufacturers Illig, Macpac helped develop a new rewind system for their machines. 2013 saw Macpac install the first Illig 74 down-stacking machine ever made incorporating this new design, which enabled a reduction of tooling costs without compromising on production efficiencies.
Innovation at the core….
Macpac said innovation is at the centre of its ethos, evidenced with a plethora of award wins.
In 2000, Macpac won both the Starpack Gold Award for its packaging design to house a carbon monoxide detector, and a Bronze Award for technical innovation.
In 2014 the business picked up another Starpack Award – this time Silver – for a patented clam pack design called Surecel which offered a range of high security, tamper-evident clam packs, without the requirement for specialist machines to close the packs, nor scissors to open them.
During 2015 Macpac received a Starpack Bronze Award for Snap In, another patented solution. This design offered the opportunity to lock a thermoformed part to another substrate, such as board or acetate sleeve, and was used for the Orchid retail market in Tesco.
A year later the firm claimed the Best Innovation Award at the 2016 Gro South Horticultural show for its Large Letter Pack design, which enables plants to be sent through the post at the Royal Mail’s Large Letter rate.
In 2020 Macpac won the Special Award for Covid 19 Response at the Railway Industry Awards. This was for the design and manufacture of thermoformed visors that could be fitted over hard hats, which were produced in record time for the Network Rail workforce to use during the height of the pandemic. The designing, prototyping, manufacturing of tooling and then forming of the visors took place over the Easter Holiday weekend, whilst adapting to new working rules introduced during that period.
Macpac added a further string to its bow in 2022 by installing the first down-stacking machine with punch and die capabilities in the UK.
The company said a ‘major attraction’ to Macpac is its personal attention to detail, working with customers to ensure they understand the initial brief and meet the needs relating to bespoke design, budget, and sustainability. From initial concept to finished design and manufacturing of tooling all under one roof, Macpac added that it has the flexibility to manufacture from as little as 1,000 units up to many millions.
In 2023 Macpac is 50 years young – with passion and family values described as still being at its core. The business revealed it is celebrating half a century of ‘proven dedication’ in design and manufacture, and is very much looking forward to what exciting new challenges lie ahead.