Although the public has widely supported the switch to sustainable forms of pack materials, more adoption of appropriate machinery is required to allow greater uptake of eco-conscious options. Bill Anderson, regional sales manager for Scotland and Northern Ireland at ULMA Packaging UK, discusses the paradigm shift required to embrace this technology.
IT is common knowledge that plastic materials that cannot be recycled hold a negative reputation amongst consumers. This growing dislike has led to manufacturers developing forms of packaging that can be sustainably disposed of to lower their negative impact.
As shown by the research conducted by management consultants McKinsey, the public are pushing for more brands to embrace high-quality sustainable wrappings over alternatives.
This means that the packaging industry has a simple challenge to conquer to create greener supply chains.
Upon their development, sustainable methods of packaging would be phased into the production line in place of unrecyclable plastics. In turn, this would lead to happier customers while reducing a brands negative impact on the environment – a win-win solution.
The will of the public may be an encouraging incentive for businesses to make the necessary switch to more eco-friendly solutions, but another motivator comes in the form of the Plastic Packaging Tax.
Having come into effect on the 6th of April 2022, companies will now have to pay a hefty price of £200 per tonne of plastic that contains less than 30% recycled matter. This bill could start to build into a substantial sum, putting a preventable strain on brands.
Sustainable methods of packaging
What makes some plastics unrecyclable is the fact that they contain several layers of different products which needs to be separated to make them eco-friendly. This process can take place at 87 specialist facilities in the UK, otherwise they are dumped at landfill.
Current sustainable forms of packaging that are available to businesses, including mono-PP or mono-PE laminates, can avoid this issue due to only containing a single layer of recyclable plastic.
The issue rises in the fact that many forms of sustainable packaging are not compatible with existing machinery on production lines.
Although the fact that mono-material films are made from a single layer of plastic is a benefit during the recycling process, it can pose an issue due to its narrower optimal sealing range.
Many machines that are currently on the factory floor cannot work between these dimensions, meaning a multitude of issues could arise if businesses do not realise. A primary issue arising from this is that the packaging would not be properly sealed, resulting in the food product within becoming compromised and a potential danger to the end-user. As well as this, the merchandise may be rejected by retailers, directly ensuing in added wastage and costs.
The technology
The issue of sealing the product proposes a difficult obstacle for the packaging industry during a time of heightened public demand and outcry. It is crucial that machinery developers work together with manufacturers to deliver this necessary technology and help facilitate this green transition.
As the narrow optimal sealing range is a major deterrent stopping brands from using materials such as mono-material films to package their products, sealing technology such as the ULMA BETTER-SEAL have been developed to address this issue. Solutions such as these ensure the stability and accuracy of the temperatures of machine sealing elements, ensuring that packaging is correctly closed to protect the product within.
An added benefit to this type of technology is that it can be fitted to existing horizontal flow-wrapping machinery, eliminating the costly and unnecessary expense of buying whole new lines to accommodate this upgrade.
These technological advancements allow businesses to make the vital change from plastics that cannot be easily recycled to products that satisfy end-user sustainability needs. To assist and encourage businesses to make environmentally friendly changes, ULMA launched #ULMAweCare, a sustainable pledge to help create technology that will assist brands fulfil their eco-friendly goals.
The paradigm shift needed within the packaging industry to accommodate the change to sustainable materials.
With innovations within the green sector continuing to be developed, the challenge falls to the packaging industry to create innovative technology that will ultimately help make businesses sustainable plans a reality.
These technological advancements mirror the wants and needs of end users and are a needed step towards more eco-friendly practices that have rapidly gone from a consideration to a priority.
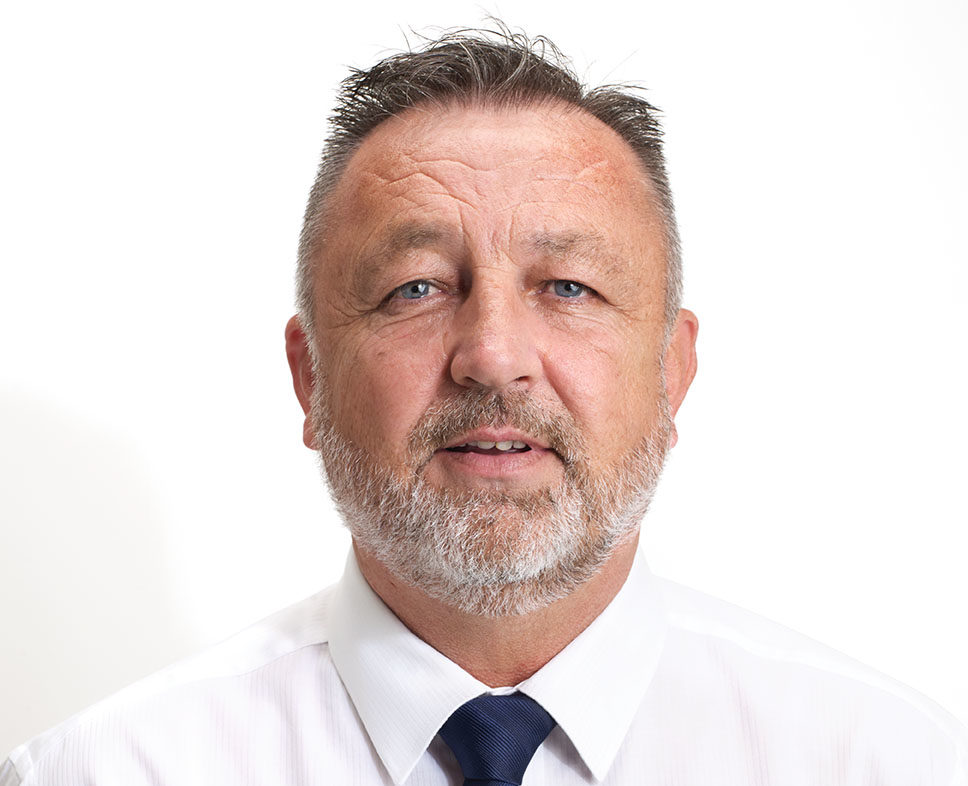