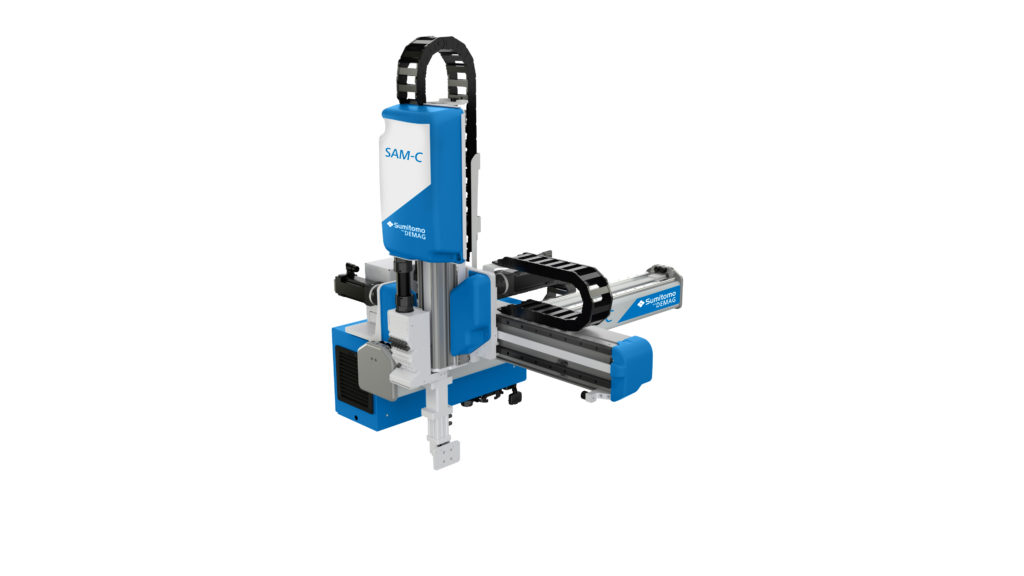
Nigel Flowers, MD of Sumitomo Demag UK, explores the impact of the pandemic on automation trends within the injection moulding sector
THE pandemic has amplified the focus on productivity and forced injection moulding decision makers to reconsider how automation and digitalised technologies can facilitate working smarter. Rather than a complete pivot, automation was already quite commonplace; especially among moulders producing components for the medical, healthcare, aerospace, automotive, electronics and packaging sectors.
Scalable, flexible units are in greatest demand. It’s why the Group launched the SAM (Sumitomo. Automation. Machine) robot series at Fakuma last year. With travel restrictions lifted, the 2022 K Show will be the first unveiling to the international audience.
The two ‘handle & place’ SAM-C robots launched to-date are designed specifically for injection moulding machines with clamping force sizes between 50 and 500 tons, and for standard applications with cycle times of 10 seconds and higher. So primarily for the transfer of parts, and insertion of loads, applying labels etc.
Automation like this can help customers to address the acute staffing shortages. Although labour was a challenge before the pandemic, filling certain jobs is becoming ever more challenging. Jobs being vacated by the baby boomers (which accounts for over 25% of the workforce in some territories) are not attracting the Millennials and Gen Z’s, which is another pressure on top of escalating material prices and supply chain issues.
Robotics can help make customer applications run faster and more cost-effectively. With take-out times of 0.5 seconds or less, it can sometimes be quicker and more productive to use a robot to remove parts than to let them fall under gravity.
Notably, remote machine monitoring was the hallmark of the pandemic. The ability to take live data from moulding machines and use this to inform operational decisions and make process improvements has induced greater trust and a change in mindset about remote access tools.
Interest in monitoring critical components in machinery is also accelerating. The company recently unveiled a series of permanent conditional monitoring systems. These can be used to determine the wear and tear on injection moulding machines, thus enabling earlier detection and allowing for the pre-planning of maintenance costs with a greater degree of accuracy.
Currently the company is focusing efforts are on real time detection of abrasion and wear to the screw, the plasticising cylinder and the ball screws on all-electric injection moulding machines. The ultimate goal is full monitoring of all critical components prone to wear.
As businesses begin the recovery process, Sumitomo (SHI) Demag is anticipating another leap forward in automation investments and digitalisation. By utilising automation, moulders can minimise their footprint, yet increase their machine estate; enabling them to boost production capacity, repeatable precision, component quality and efficiency and consequently reduce defects and waste.
The company anticipates rolling out additional robot kinematics and adapted options as early as K-2022 and further expanding the SAM platform within this short timeframe.