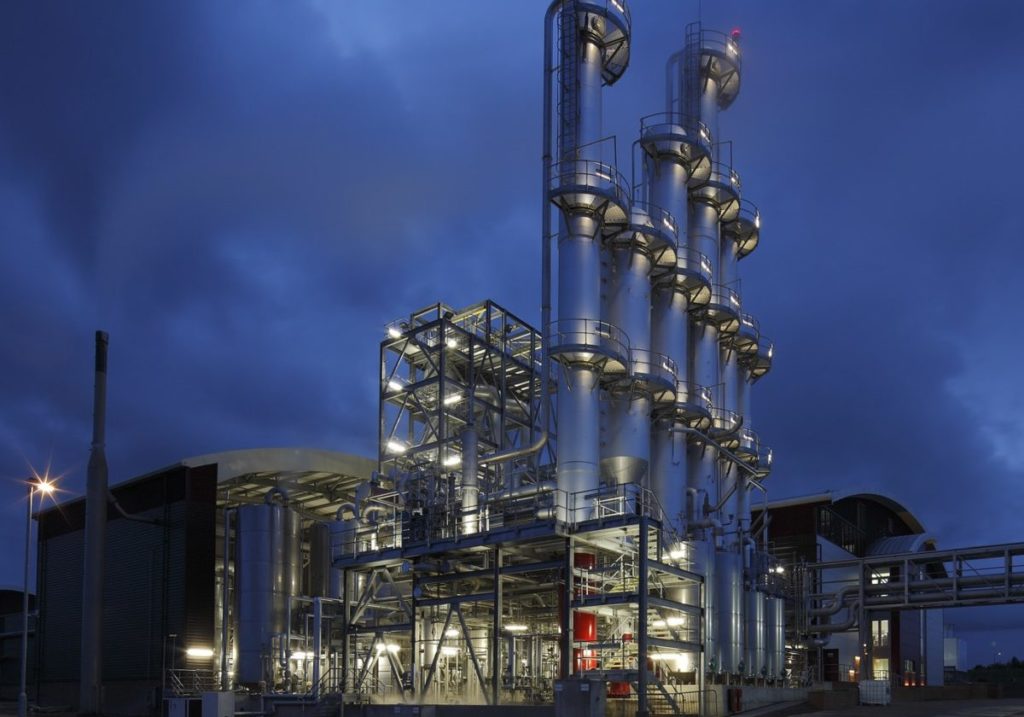
AN Irish spirits brand has had a custom-designed distilling line installed by Frilli, part of the Della Toffola Group and sister company to AVE UK.
Frilli revealed that, since the move, the grain distillery has ‘only ever made Grade 1 spirits’.
Chief operational officer, Filippo Cannoni, added, “All the equipment was delivered, installed and commissioned within the agreed timelines. And when it comes to the conversion of starch to alcohol, the efficiency of the plant is among the best in the industry.”
The spirit is a triple blend whiskey, combining grain (from wheat), malt (distilled from malted barley) and pot whiskey (half-and-half barley and malted barley). The distiller wanted to gain ‘direct control’ over the grain, to avoid an ongoing cost in outsourced supply and ensure consistency of quality.
The business turned to Frilli for support in developing a new grain distillery comprising the characteristic Coffey (or column) stills.
Frilli took responsibility for the mashing, fermentation and distillation stages. Filippo Cannoni explained, “The distiller initially engaged us with the front-end and then base engineering. This was the high-level process concept: the kind of equipment, rough sizing and process flow diagram which would achieve the necessary outcomes in terms of chemistry and organoleptics.”
The next stage was detailed engineering to turn the concepts into an ‘executive’ project. “The flow diagram was transformed into a detailed process and instrument diagram, complete with precise sizing, pressure, and so on,” Filippo added. “Then we needed to manufacture the key equipment, including the column stills, heat exchangers and distillation trays, as well as overseeing the third-party manufacture of additional equipment to meet our specifications.”
The installation, fine-tuning and commissioning took just a few months, with the most challenging and time-consuming part of the process described as revolving around the need to obtain a close match between the character of the new whiskey and that specified by the client.
“The distillery operates to very high levels of efficiency,” Filippo said. “Process guarantees might stipulate the amount of grain, energy, water and overall process yield, so duplicating the sample was not easy.”
AVE UK represents Italian-based Frilli and other Della Toffola Group companies in the UK and Ireland. AVE’s sales director Steve Bradley understands the relationship between this type of fine-tuning and the way an installation is calibrated. “The key point is to build in high levels of flexibility in order to allow these finer adjustments to take place, to ensure the client is completely satisfied with the end product,” he revealed.
“Before 2010, the company (Frilli) had built its first grain distillery in Scotland. The team introduced a lot of innovation, even in the confines of the fairly traditional Scottish whisky industry, and this became a benchmark for distillers internationally.”
One area of innovation is the level of automation in the grain distillery. Steve added, “The start-up and shutdown procedures are fully automated, which is not always the case for distilleries. Keeping the process 100% fully controlled enables the same product quality and character to be replicated every day.
“In this case, automation is not about reducing manpower, but about ensuring the consistency of the final product.”
Filippo revealed the approach has paid dividends. “Spirits can be classified as Grades 1, 2 and 3. Since installation, the grain distillery has only ever made Grade 1 spirits.
“There was an allowance in the contract for a certain amount of Grade 2 and Grade 3 spirits in the initial stages. But our installation has only ever made Grade 1 product, right from the very start.”
Hygiene and efficient energy use were also cited as major considerations. Energy recovery systems have been integrated into the grain distillery to ensure no energy is wasted.
“The aim is to deliver the required results at as low a temperature as possible, but also to maximise the use of that energy,” Filippo explained. “For instance, one column still shares energy with the next, and so on, in a cascade effect, to ensure that none is wasted.”
Frilli has already made a further contribution to the site, having designed an ethanol recovery plant, and there are plans for further collaboration in the future.