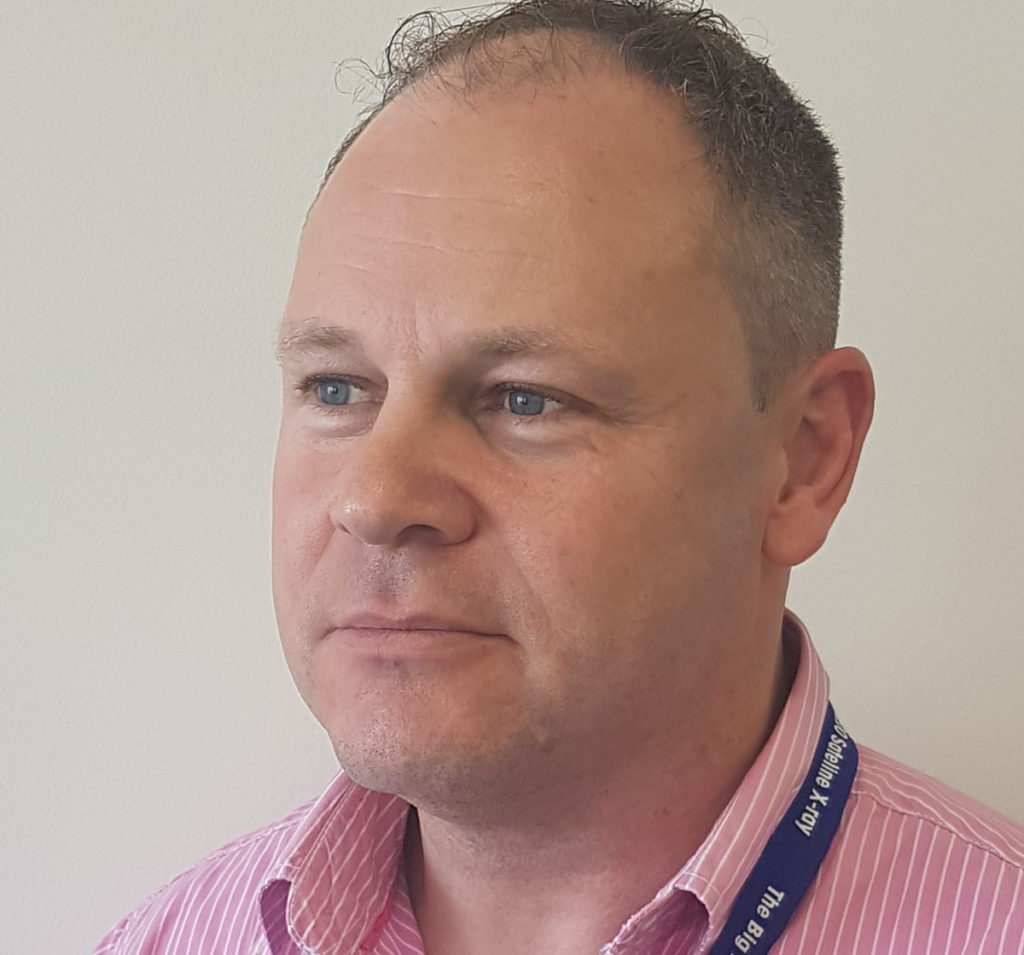
Audits are a reality of business for contract packers in the food supply chain, testing their ability to adapt to the requirements of different customer and compliance demands. Product inspection technology underpins that capability, but must be implemented and managed correctly, explains Niall McRory, global key account manager, Mettler-Toledo product inspection division.
For a contract packer, audits can come from many directions. Brand owners, retailers, food or packaging manufacturers and standards/certification bodies as well as regulators all have an interest in the robustness and integrity of your Quality Management System. For some of these parties, it is more than an interest – it is a stake.
Whoever instigates the audit, and whatever their relationship is to the co-packer, what they are looking for is evidence that:
- The contract packer has soundly thought through the quality management or food safety program in place
- The program has been created with due consideration of internal Hazard Analysis and Critical Control Point (HACCP)/Hazard Analysis and Risk-Based Preventative Controls (HARPC) audits, to identify potential areas of risk, and put procedures and technologies such as product inspection in place to minimise those risks
- Co-packers are meeting the compliance demands of customers, retailers and regulators
- Records have been kept, demonstrating the necessary processes for monitoring, testing and maintaining production equipment that ensure quality and food safety.
Product Inspection equipment such as checkweighing, metal detection, x-ray and vision inspection is the friend of the contract packer when it comes to audit time. By inspecting products and identifying problems such as foreign body contaminants, it underpins the entire quality and safety management program.
Through constant data collection, it also provides an audit trail of production, testing and maintenance activity – a treasure trove of information for auditors, customers and co-packers alike, especially in light of approaching digital supply chain and track and trace requirements.
But product inspection needs to be done right. In contract packing environments, where there can be multiple job changeovers, serving numerous customers and compliance frameworks, the added layers of complexity make this even more paramount. Doing it right involves these five key steps in implementing product inspection, all of which will help you prepare for and pass audits:
- Integrate advanced product inspection technologies
As a contract packer, you need to be flexible to accommodate different formats, sizes and types of products and packaging. The more agile and easily configured your product inspection equipment is, the better it will be able to meet the needs of retailers, manufacturers and brand owners. Advanced product inspection technologies generally make it possible for product set-up and job changeover to be automated, saving valuable time, and ensuring that parameters for each set-up support the compliance demands of that customer or regulatory framework. The equipment should also be capable of real-time monitoring and recording of all inspection activities, providing an audit trail of data to support compliance.
- Data collection and connectivity
Data records used to be kept on paper in lever-arch files. More recently, they could be extracted from equipment using a USB stick. Neither situation is ideal for responding to an audit, especially if there has been little warning given to the co-packer. Connectivity makes responding to the demands of an auditor much quicker and simpler. Product inspection equipment gathers data during operation, and with data management software, such as Mettler-Toledo’s ProdX, this wealth of information, including data from remote sites, can be sorted and arranged as needed. It can be electronically transmitted into MES/ERP systems and provide the basis for digital supply chain interaction and track & trace capabilities. From an auditor’s perspective, the use of digital data collection methods means they get excellent data in the format they require as soon as they need it.
- Testing procedures
Evidence of regular and effective testing will demonstrate to the auditor that your product inspection equipment has been fully functional and continuously optimised to do the job you bought it for. The more regularly a machine is tested, the more certain you can be that good products are leaving the factory – products that won’t need to be recalled at great loss at some later stage. While testing has traditionally been a manual process, it can increasingly be carried out using automation, saving time and potential human error. Advanced product inspection solutions, such as Mettler-Toledo Safeline metal detection systems also have a Reduced Test Mode, in which an on-board monitoring system continuously checks the performance of the metal detector, reducing the frequency of routine performance test requirements.
- Training/employees
No quality assurance or food safety program can succeed without the participation of employees that understand the imperatives behind it, appreciate how important strict observance is, and have the skills to perform their part in the process competently and consistently. Passing an audit successfully depends upon having these employees too. Although the development of more automated machinery has made product inspection technology increasingly easy to use, operators employed in co-packing still need to be knowledgeable and well-trained, capable of adapting to fast-changing scenarios and multiple customer and compliance demands. Partnering with the right equipment supplier will give you access to knowledgeable experts who can support you in training your staff to required levels.
- Preventative maintenance
Similar to regular testing, preventative maintenance keeps product inspection equipment running at optimum levels of performance and prevents breakdowns and production line delays. Co-packers can address the issue in two ways; Firstly, by having their own skilled technical department to deal with scheduled maintenance checks and repairs as needed. Secondly, by partnering with machinery suppliers that have reliable equipment and the scale of support, both engineers in the field and remotely, that is required to maximise uptime of highly sophisticated inspection systems. Consistent and reliable operation of production line machinery is good for business, and a head-start towards successful audit performance.