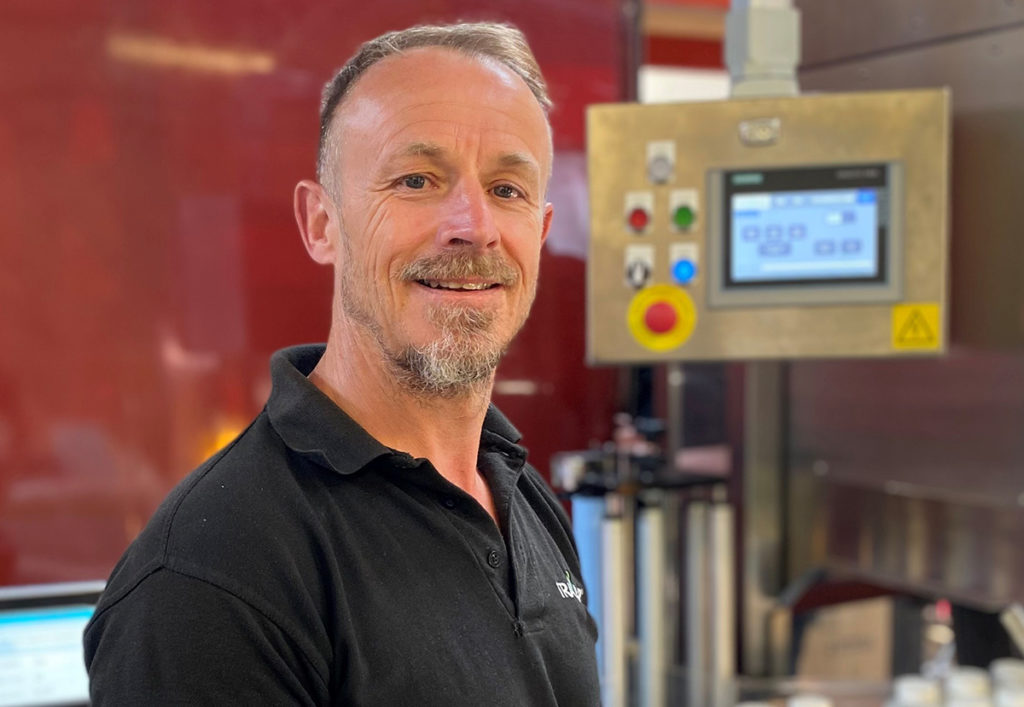
Producers seeking sustainable alternatives to shrink wrapping should stop to consider the true benefits of the packaging they select, says Martin Leeming, CEO of TrakRap
SHRINK wrapping is high on energy consumption and low on environmental sustainability, so it is understandable that producers are actively seeking alternative packaging options.
When looking to introduce more sustainable packaging, the first decision for many manufacturers has been to remove plastic. But the reality is that, despite their noble intentions, many will almost certainly have increased the carbon footprint of their products by doing this.
This is because they have focused on the end material and not the footprint involved in production.
Take the example of a switch to cardboard packaging. Cardboard is often heralded as a more environmentally friendly alternative to plastic because it is biodegradable, but it has a huge carbon footprint.
To produce corrugated cardboard, trees need to be harvested, shipped to pulp mills, pulped, formed, pressed, dried and rolled, before being sent to corrugating plants and made into cardboard.
This process demands an enormous amount of energy. Worse still, when the cardboard decomposes carbon is released back into the atmosphere, contributing to rising global temperatures.
The end result is that businesses which simply swap packaging materials so they can claim to have reduced plastic are often actually doubling their carbon impact in doing so.
A great example of this contradictory action is the banning of plastic carrier bags in UK supermarkets and replacing them with paper alternatives.
What was not taken into account was that the carbon footprint of a paper bag is approximately five times larger than that of a plastic bag. So, supermarkets simply swapped one problem for another.
Genuinely sustainable solutions are available for manufacturers and processors keen to explore alternative packaging in a bid to reduce their carbon footprint. The first step is to move to alternative packaging methods which eliminate the use of heat tunnels from the packaging process entirely.
For example, orbital wrapping systems are a great alternative to shrink wrap and are becoming more commonly used, particularly in food and drink manufacturing factories.
Systems such as TrakRap use ‘cold wrap’ technology – a process where an ultra-thin stretch of film that is 100% recyclable and lightweight is applied directly to products.
No heat is required to wrap and protect the items, saving as much as 90% energy when compared to shrink wrapping.
To further enhance the sustainability benefits, these systems can also be used in conjunction with innovative packaging solutions such as corrugate or recyclable rPET trays. These products use up to 70% less cartonboard in their production than traditional trays and are 100% recyclable.
There’s a strong argument that truly sustainable packaging means making the producer and user fully accountable for the way we treat packaging throughout its life.
This was the driving force behind the development of GreenRap and the ‘GreenSac’. This distinctive green coloured plastic allows TrakRap wrap to be easily identified and separated when it is removed, then simply placed in the GreenSac and returned as part of a closed loop system.
Sustainability is rightly a major consideration for businesses – and it can be easily achieved in the packaging process with the implementation of the right technology.