With the constant evolution and increasing use of automated handling systems, the impact of pallet quality in such systems becomes of critical importance, writes Dianne Carroll, commercial director at LPR UK and Ireland
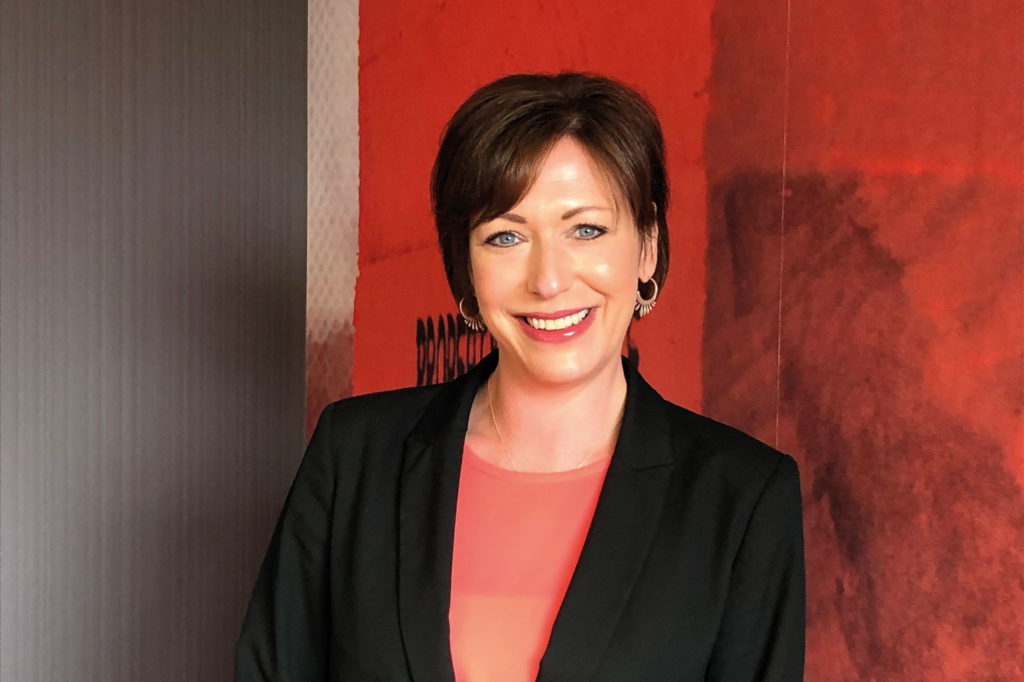
WITH almost all goods, especially those in the fast-moving consumer goods (FMCG) sector, being moved on pallets, it is no surprise that there has been a steady growth in the use of automated pallet-handling systems.
Indeed, market intelligence firm Interact Analysis predicts that the warehouse automation market will grow at a compound annual growth rate (CAGR) of 12.6% over the next five years. These systems range from conveyors, palletisers and pallet sorting and repair units, to autonomous forklifts and stacker cranes.
Not all pallets are designed to be used within automated handling machinery – indeed, using unsuitable or low quality pallets can even cause jams, leading to costly downtime.
The default setting for many automated systems when jammed, is to stop until a human technician can resolve the issue. Such stoppages can have a significant effect in a highly automated warehouse where lengthy delays and missed shipments can create huge costs.
According to a recent survey carried out in the USA by Virginia Tech University, Modern Materials Handling and Peerless Research Group, issues with pallets can include: poor quality bottom boards that cause jams or faults; missing or damaged components that cause the improper placement of unit loads; inconsistent pallet dimensions; and product damage.
The biggest pallet-related issues identified by the survey include loose or broken pallet components getting caught in rollers (21% of respondents say this happens daily or weekly); incorrect placement of bottom deckboards leading to split or damaged pallets, poor quality or missing bottom boards and other missing or damaged components (25%).
Overall pallet quality was noted to be a major culprit. A company using low-quality pallets in a highly efficient, fully automated distribution centre, for example, is bound to run into problems.
These findings mirror LPR’s own experiences. Through working with our customers, we have found that chips and splinters in pallets can affect the efficiency of automated handling systems, causing downtime while they are rectified. Pallets can also become damaged whilst being loaded onto forklift trucks. This can lead to additional time being required to sort the pallets ahead of loading into automation.
What can be done to combat these issues? Selecting good quality pallets provided by a trusted pallet pooler is a good place to start, for example, LPR will work with you to understand your pallet use, and have extensive experience of pallet usage in automation.
Additionally, quality checks can be undertaken to ensure that issues with pallets are identified and rectified early. Finally, forklift operators can be retrained to minimise damage to pallets caused during handling.
Pallet construction is constantly being re-evaluated. At LPR we have phased-out the use of composite blocks in our pallets. Indeed, we identified as early as 2010 that solid wood blocks are significantly stronger, more durable and more environmentally friendly (as they are free from formaldehydes). Composite blocks cause issues in automated handling systems owing to expansion due to water ingress and misalignment as the blocks become twisted.
Given that automated pallet handling systems represent a significant capital investment to businesses, suitable consideration should be given to the humble pallet – selecting the right one will save your business both time and money.