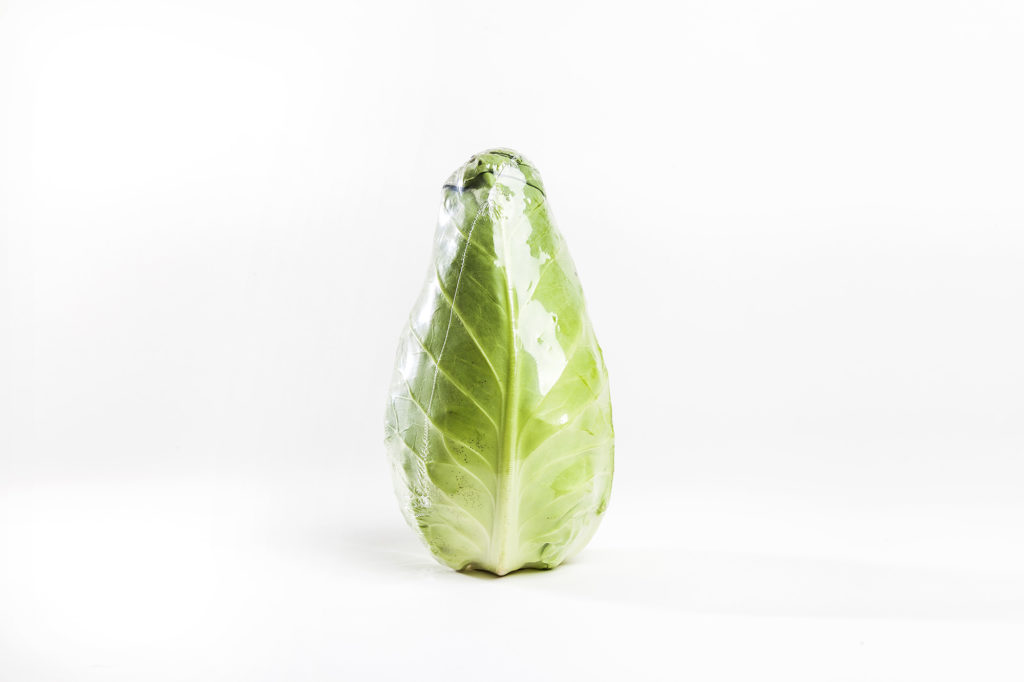
YORKSHIRE Packaging Systems (YPS) will relocate to a new premises by the end of 2020 after having to erect a temporary storage unit to keep up with demand at their current headquarters.
In keeping with its name, the business is remaining in Yorkshire – swapping Dewsbury for Brighouse, allowing for better connectivity with clients across the UK, thanks to its place on the M62 corridor.
“It’s 50% bigger than where we are now,” Olivia Routledge told Packaging Scotland. “We’ve been growing consistently over the last decade and our current premises is bursting at the seams!”
Storage is particularly important to the family-run business with the popularity of its call off order system, which allows customers to reserve shrink wrap and have it stored in Yorkshire Packaging’s warehouse to be delivered in required amounts on a same or next day basis – with the customer only paying for however much they take, rather than a reservation or full line fee.
Olivia explained that the system is a popular one, with existing clients often not knowing of its existence but immediately taking advantage of it once told. Customer satisfaction is a pivotal part of the business, with an annual repeat order figure ranging from 40-45% each year. Olivia insists that won’t just seek to benefit customers from a storage point of view.
Olivia added, “We’ve got so many customers taking advantage of the call off order system, that we’ve got a lot of stock with a lot of machines on site, and it’s really important that we’ve got a great demonstration area for customers to come round and do trials and demos – so with the new premises we’re just wanting to reflect who we are a bit better as well; something a bit smarter and sleeker. So that’s the plan.”
The move also comes at a time in which Yorkshire Packaging have released, and are exploring, new ventures in both products and services.
“With the expansion it’s not just different markets but different products, so stretch wrapping is brand new to us, it came earlier this year,” Olivia said.
YPS also offers the B-NAT shrink film, manufactured by Bollore and Braskem, which comprises 46%polyethene produced from sugarcane ethylene, with the entire film being fully recyclable at household level.
It is formed in a process where the sugarcane is ‘squeezed’ five times. The first two squeezes produce pure sugar for the food supply chain. The last three squeezes produce an ethanol bi-product which is unfit for human consumption and is processed into the base for B-NAT shrink film, rather than being wasted.
Harvested in Brazil, the operation barely impacts on any arable land, with YPS billing it as the first polyolefin material to address the issue of the majority of polyolefin ending in landfill.
The technology comes alongside further sustainability pushes being eyed by the company. Olivia revealed, “We’re now looking into offering a baling machine service. So customers when they’ve got a shrink wrapping operation, there’s a certain amount of plastic waste that comes off the machinery, and we will be able to put a machine on a site that we will service, maintain and install it, it collects the waste and gets it into a cubic tonne and every time that happens we will collect it and that is going back into a resource and completing the full circle economy.”