By Lesley Eaton, business development and marketing manager at SEEPEX
ANNUAL sales of progressive cavity pumps (PCPs) within the European food and beverage market top $100 million. Primarily used by food processors to handle delicate ingredients, they can also make a real difference in other areas, including waste removal.
Most food plants generate by-products, which processors must remove efficiently and hygienically. While the majority use a combination of traditional methods such as manual removal, blown air systems and flumes, these incur high running costs. PCPs offer an alternative – enclosed piped systems which remove solid waste from both high care and low risk areas, without compromising hygiene standards.
Chopping with pumping
As well as handling extremely viscous products which do not flow, SEEPEX has designed a progressive cavity pump that can chop and pump food waste containing up to 40% dry solids in the same unit, without the need to add water. This open-hopper PCP features an auger feed into fixed and rotating knives, producing a lower volume of easy-to-handle waste. Discarded products, defective raw materials, trimmings and rejects can be handled in a single system, enabling pre-treatment and source segregation of differing waste and by-products. Wet coleslaw, whole raw potatoes, whole chickens and trimmings can all be treated efficiently and hygienically within a single unit, delivering low-cost waste removal while preserving the highest residual value.
PCPs in action
Natures Way Foods is a leading manufacturer of fresh convenient foods, including ready-to-eat fruit products. Its production process generates peelings, cores and stone waste, which must be removed from production areas. The company’s existing systems were not able to handle the volume or variable nature of the different fruit types or process methods, so SEEPEX installed PC pumps from the BTM range linked to the output of automated peelers via ultrasonic ‘smart’ level controls. Trimmings are collected in tote bins before being tipped into a standalone system. This comprises a customised reception hopper linked to a vertical grinder and PC pump combination, which grinds the waste and pumps it through enclosed pipework to the waste reception area. A PC pump with large reception hopper, bridge breaker and integral knives acts as a back-up and provides additional capacity for hand-peeled fruit waste.
Bespoke solutions
All SEEPEX waste pumped systems are individually specified, featuring low energy requirements and needing no additional water. Their versatility and modular design enables them to cope with most food waste products, delivering cost savings and improved hygiene for today’s food processors.
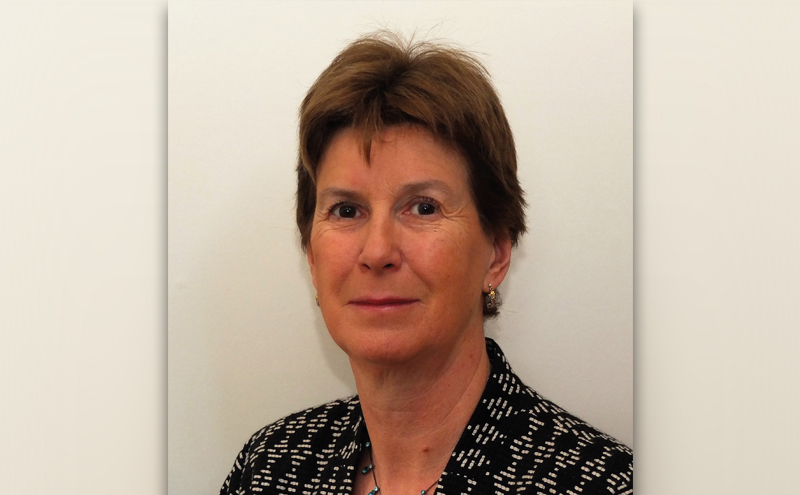