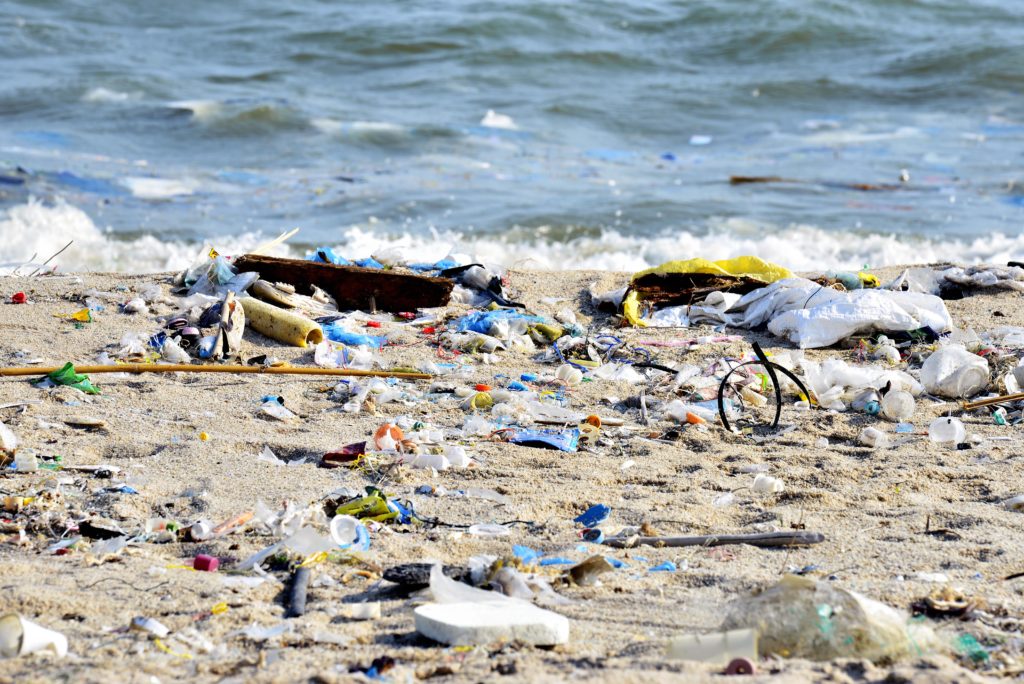
What are we doing about plastic wrapped consumer goods? With the use of polypropylene films under attack, sales and marketing director Tony McDonald of flow wrapping machinery manufacturer Ilapak is being asked this question more often. Here, he debates the ban of all plastics following Ilapak’s latest machine developments to successfully run new sustainable polymer-based films.
A bold New Year’s resolution from the Prime Minister was an undertaking to eliminate all avoidable plastics waste within 25 years. Theresa May even suggested that supermarkets should establish aisles free from plastics packaging – or any packaging at all, for that matter.
We clearly have to discount scurrilous suggestions that Mrs May was desperately seeking a cause and a proposal which over half the electorate might actually rally around.
As David Attenborough demonstrated eloquently late last year on the BBC’s Blue Planet II programme, the issue of ocean plastics is serious and urgent. Europe’s contribution to the problem is less clear. Here in the UK, we need to develop more responsible approaches to all types of waste, including plastics. But what should ‘responsibility’ mean for UK consumers and supply chains?
If consumers want to shop for unpackaged food, of course, they should be able to do that. If retailers want to ban plastic or plastics-containing packaging, that is clearly their prerogative. But we should be wary of putting ourselves in a situation where it is ‘the tail wagging the dog’. In other words, the performance of plastics has developed over many decades. Weights have been optimised. A first important point to make here is that these materials are there for a reason: they protect food and help keep it fresh for longer.
Most famously, perhaps, a film-wrapped cucumber will remain in good condition for significantly longer than one left unwrapped. At the same time, the Waste and Resources Action Programme (WRAP) quotes research which shows that around ten times more energy and materials are locked up in goods, including foods, than in the packaging surrounding them.
Recently, I’ve been approached at industry events and asked what we, as a company, are ‘doing about plastics’. The implied question is: ‘How are you going to eliminate them?’ But my answer is: ‘What are we doing about plastics? Helping to make them better.’ And I mean ‘better’ both in terms of performance and overall sustainability.
A second, and equally important, point worth spelling out is that sustainable alternative materials do exist, and continue to be optimised, just as standard films have themselves gone through a process of optimisation.
It is true that some aspects of this focus on environmental responsibility appear to be cyclical. I recall, almost exactly 10 years ago, a flurry of activity around alternative films. We trialled many new materials on our flow wrapping machines at that time, too. Much of that activity faded as financial and economic crises took hold, and some may be holding their breath hoping that the current scrutiny of plastics will fade in the same way.
But I believe there are differences between 2008 and now. Attitudes have hardened among ministers, consumers and across the supply chain. At the same time, materials options have moved on considerably over the intervening decade. Brand-owners and retailers (some retailers, at least) are more prepared to invest in innovation and, last but not least, machinery manufacturers are working more closely with them to make a success of these sustainable options.
Whether in the context of re-use, recycling or the use of renewable resources, the concept of the circular economy has caught the imagination of a growing numbers of business leaders, as well as political leaders, across different supply chains at European and global level.
Over the past few months, we have been working with innovative UK materials manufacturer Four04 to ensure that its compostable EVAP film can run on our Vegatronic vertical bagging machine packing nuts for a major retailer. The film, which is engineered to offer a high moisture vapour transmission rate (MVTR) whilst retaining a gas barrier, has quite different heat sealing characteristics to a standard bagging film such as oriented polypropylene (OPP). Like the cucumber, these nuts would dehydrate and spoil quickly in a sub-optimal environment.

To successfully run the EVAP film with 100% seal quality, Ilapak’s R&D team have made considerable design changes to their Vegatronic bagger and are now working to identify other opportunities for running this and similar polymer-based compostable films on other machines and in other applications.

The environmental impact of food waste as a result of not using plastics in packaging would be simply unimaginable. Retail chains are obviously within their rights to drop all plastics packaging like a hot potato in the belief that this is a smart move for their brand. But food and drink manufacturers which innovate, for example, with sustainable polymer-based packaging could be making a much smarter and more long-sighted decision.