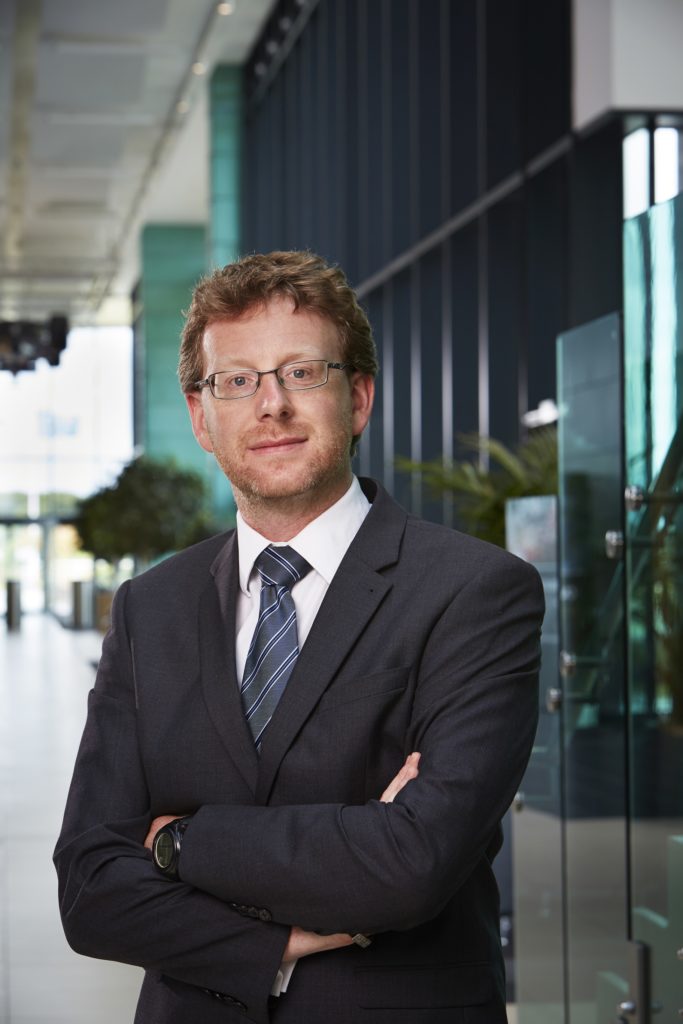
PACKAGING Scotland will be chairing a learning hub session focusing on the benefits of automation and robotics in the food and drink industry at the upcoming PPMA Show.
Jeremy Hadall, Chief Technologist – Robotics & Automation – The Manufacturing Technology Centre, will be busting some myths around the subject and explaining how we’re nowhere near close to replacing every manufacturing employee with a robot.
Speaking ahead of the event, Jeremy answered some key questions on the topic.
Q) What are some of the most common myths and misconceptions regarding robotics and automation?
A) The most common myth is that robots will replace humans and take away their jobs. This is not necessarily the case. Studies show that while robots may replace humans in the short term, employees are typically deployed to other higher value roles, driving value to the company and workforce. The benefits are two-fold. Robots are more productive and create more value for the organisation, driving output and improving profitability. This results in a greater need for higher skilled individuals to join the organisation, driving employment opportunities. Finally, this can also have a positive effect on the economy.
Another misconception of robots is that they are dangerous. In reality, they should not be if the appropriate risk assessment and mitigations are carried out. If these are carried out, robots of any type (including traditional industrial and collaborative robot systems – robots that are designed to operate collaboratively with humans within a defined workspace) will be safe to operators if they then use them correctly.
Finally, a big misconception is that people tend to think robots are expensive. To understand the return on investment, manufacturers need to assess the long-term payback. Robots are designed to operate over a long period of time, so ROI should reflect this. Often the short-term payback is the focus but by understanding the full capabilities of robotic automation, manufacturers can expand the possibilities of robotic deployment within the factory or manufacturing site. For example, robots can operate 24 hours a day, 7 days a week with almost no downtime, driving an increase in output and profitability. If demand changes or new products are introduced to the production line, a robot can be quickly adapted and reconfigured – for a true ROI, manufacturers need to consider these possibilities and not just focus on the short-term payback.
Q) How quickly/slowly has the packaging industry been embracing this technology?
A) While the uptake of robotic automation in the packaging industry has not been the quickest, it is by no means the slowest. The automotive industry continues to be the biggest investor in robotic equipment. For example, in terms of robot sales, more than half is distributed to the automotive industry, with the remainder spread across a wide mix of industries. However, the processing and packaging industry is among the top three users of robotic technology despite the huge amount of untapped potential for a greater uptake within the industry.
Q) What are the biggest advantages of using robotics/automation compared with more traditional methods?
A) Speed, consistency of output and productivity are among the biggest advantages of using robotics/automation. Robots can also potentially take up a lot less space. They don’t need breaks and can be operational 24 hours a day, 7 days a week. Robots can also offer advantages to the workforce by improving working conditions and removing workplace injuries. For example, a robot replacing manual operations to move heavy boxes removes the risk of human strain and injury.
Robots also offer long-term cost savings and can be used for applications replacing low-paid manual labour, driving more high value roles for the workforce.
Q) Are they expensive?
A) An initial capital outlay may look quite expensive but it is important for manufacturers to consider the true return on investment through long-term planning as the initial investment can be considerably offset by its long-term advantages.
Q) How easy is it to set up robotics and is there much on-going maintenance?
A) In theory, relatively simple. Installing a robot is not difficult, but its integration with the wider environment requires more consideration. Manufacturers need to assess what the technology will be connected to and how products or parts will be transported to and from the robot. To get the full benefits available, consideration of the tooling parts and wider production line must be assessed to ensure ease of integration and operation.
As with any machine, robotics will need maintenance but thanks to the advances in the technology it is designed to operate for extended periods of time (30,000+ hours) without failures.
Q) What are the risks associated with robotics and automation and how are these minimised/alleviated?
A) Manufacturers need to understand what they are trying to achieve with an automated process. There is often a risk of rushing to automate a process when it may not be the best solution. The best way to mitigate that is to thoroughly understand the process before you try to automate. By assessing the production line, manufacturers can work with robotic suppliers to pinpoint the areas of the production line best suited for automation.
In addition, robots can be big, heavy pieces of equipment so health and safety risk assessments are critical. By performing these assessments, risks can be eliminated.
Q) What advances have you seen in robotics and automation over the course of your career?
A) Collaborative robots have been very disruptive in the market place, but they are often limited in speed and payload. The next step is making larger scale robots that can operate in collaboration with humans. Advances in programming have also resulted in robots being easier to program and use and this will continue with the introduction of artificial intelligence and machine learning.
Q) What do you see as the future for robotics and automation in a packaging context?
A) I’d expect to see more collaborative applications where humans and robots work closely together and robots that can sense and react rather than being told to perform a task. In the wider factory network, the Industry 4.0 concept will continue to increase. The Industry is continuously researching how robots can mimic what the human hand can achieve. This will result in advances in what materials robots can interact with – further expanding the capabilities of the automated production line.
Robotics and automation: busting the myths will take place on 27 September, from 11.00 to 11.30, at the Learning Hub.