In the past few years, the issues surrounding the recyclability of one-trip packaging have been put into the spotlight in the food logistics industry. For a sector so vital to the food supply chain, ensuring a sustainable business model is crucial to obtain business longevity. Notions such as resource efficiency and waste prevention have been brought into the debate, to sit alongside issues of reducing carbon emissions.
Joanne Moss, managing director of PPS, tells Packaging Scotland about the effects that packaging can have for sustainability in the supply chain of the logistics industry. She looks at the “unique” design of their own returnable transit packaging (RTP) as well as the effects that switching from one-trip packaging to RTP can have on your business’s sustainability goals as well as bottom line.
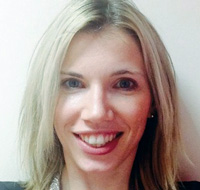
FOR the past few months, WRAP has been putting an increased emphasis on reducing supply chain packaging and improving product protection to eliminate food waste in the food retail industry.
Working with major retailers and brand manufacturers, they have been working towards improving resource efficiency and reducing waste in the UK grocery sector.
For the EU, waste prevention has also been top of the agenda in their ‘waste hierarchy’ scheme – aiming to prevent issues surrounding correct disposal by preventing waste generation at supply chain levels.
As of October 2013, the Government’s Packaging Regulations stated that re-usable packaging must be manufactured in such a way as to allow for it to be recycled at the end of use – creating a context in which the food logistics industry is forced to face issues of sustainability moving forward.
How can packaging make a contribution in the food logistics industry?
Preventative measures such as the use of returnable transit packaging (RTP) is one way in which waste prevention can be achieved at supply chain levels. Equipment is re-used on a closed-loop system, allowing transit packaging to bypass the recycle heap and be used on an ongoing basis.
In a case study, PPS chose two specific single use packaging products, namely one-way trip cardboard boxes as well as single use expanded polystyrene (EPS), and compared them to returnable, nestable plastic crates and their new ‘Re-Fresh’ fish box.
The study found that switching from single trip cardboard boxes to plastic crates produces roughly 52% less carbon emissions whilst the switch from polystyrene is even greater at 89%. A portion of cardboard boxes do end up in landfills, despite efforts to recycle. Moreover, the energy use is far greater, with longer processes involved.
Polystyrene containers fared even worse, with a longer process involving higher energy usage levels as compared to RTP, which when used on a closed loop system uses a fraction of the energy and is 100% recycled at the end of its life cycle.
New packaging technologies
In the production of returnable transit packaging, materials are continually tested in order to conform to strict regulations within the food logistics industry as well as for chemical resistance, strength and durability to ensure a long life span.
Materials including HDPE (high-density polyethylene) and PP (polypropylene) are used extensively in the manufacturing of equipment such as plastic crates, bulk bins and plastic pallets as it is the ideal material for injection moulding.
Possessing chemical and corrosive resistance, the odourless material is the optimal choice for ensuring that the packaging can be hygienically washed using food safe chemicals enabling the re-use cycle to continue at the highest quality standards.
The material is also resilient between a large span of temperature fluctuations, ensuring the high strength material can be used in various environments. This might include use in cold stores where foods are frozen or hotter climates that might be involved with citrus fruit farming.
Design features from injection moulding enable the goods to stay fresher for longer. Ventilation slots in plastic crates are ideal for freezing foods allowing the surrounding temperature to penetrate the plastic vents. The strength of material used plays a crucial part in protecting the goods in transit and storage.
The Re-Fresh box, recently launched by PPS, is a hygienic plastic tray, for full supply chain distribution of fresh fish and seafood.
With a leak-proof lid, the boxes are designed for transit and can be 100% recycled at the end of their lifecycle.
Built with stacking/nesting capabilities the boxes are designed for strength, lessening food damage and waste.
The ability to stack a number of boxes for transit was an engineering design challenge undertaken by Mergon International for the PPS Re-Fresh boxes.
Under compressive loading, buckling due to structural instability is often a significant engineering concern. To enable stacking, a bi-linear elastic-perfectly-plastic material model was developed. This model used an assumed tangent modulus so that plasticised regions strain indefinitely unless limited through redistribution of load into surrounding nonplasticised regions.
This analysis method allows for an efficient assessment of the structure’s theoretical buckling capacity. The ANSYS Suite of software was used throughout the project, including ANSYS Professional NLS and ANSYS Design Modeller.
Changing your supply structure
With the correct procedures in place, the move from recycling to re-using in the food logistics industry can be a simple process.
There are many options for making re-usable equipment work within your supply chain, every operation is different, and therefore it is vital that businesses find the solution which works for them.
As a main service provider of RTP, 95% of PPS customers experience cost savings when they switch to returnable options, typically saving 25%.
When switching from a single-use alternative, the capital expenditure involved in purchasing an equipment pool can be fairly large and somewhat off putting. Re-using saves money per trip when compared to single use alternatives due to its longevity qualities.
Yet the initial outlay of investment can prevent many businesses making the move from recycling to re-using.
However, with the option of renting or leasing, the alteration of a business’s supply chain model does not have to run the same financial risks and pitfalls.
Recycling has become the most common method used by companies to improve their green credentials. However, with the costs involved and issues surrounding viable waste disposal procedures, recycling can make sustainability a far flung goal.