SCOTTISH crisp manufacturer Mackie’s Crisps has recently installed three Ishida iTPS (Integrated Total Packaging System) at its new factory in Inchcoonans in Errol, Perthshire.
Comprising an Ishida 14 multi-head weigher and Atlas bagmaker along with a throat metal detector and thermal transfer coder, the Ishida iTPS can be controlled and monitored via an easy-to-use Remote Control Unite (RCU).
The Atlas bagmaker features double rotary jaws and superior control technology to combine fast speeds with accurate film registration and tight bag seals to minimise raw material waste, film loss and downtime for film changes.
An innovative sealing unit creates tight seals without wrinkles even during high-speed packing. Pressure, temperature and sealing time are set on the RCU to match the production speed and film characteristics, creating optimum seals. The Atlas’s product charge control reliably strips any remaining product from the seal area and also prevents product from being blown upward, while a unique auto film splice module reduces product changeover times by up to 10%
The three iTPS are situated at the end of the Mackie’s production line, each one linked to an individual flavouring station supplied by Heat & Control. This gives Mackie’s the flexibility to weigh and pack up to three different crisp varieties simultaneously, enabling the company to respond quickly to customer orders and to maintain production while one machine undergoes a product changeover.
George Taylor, Chief Executive of Mackie’s at Taypack, said, “We have around 75 SKUs and 30 different flavours so we need to be able to respond quickly and handle different requirements at the same time.”
Changeovers are easy to facilitate with individual product and pack details held in the iTPS’s memory for fast call up via the RCU. The Ishida weighers are simple to clean with hoppers easily removed and replaced without the need for tools. Each weigher has a spare set of hoppers and the hoppers are interchangeable on the machine, which keeps downtime to a minimum.
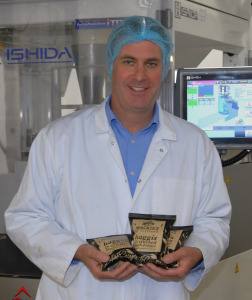
Mackie’s packs 150g, 40g and 30g packs, with the iTPS capable of handling 40g bags at up to 110 bpm (bags per minute) and 150g bags at up to 70 bpm while maintaining accuracy to within 2% of target weight. Mackie’s reports that the systems are performing extremely reliably as part of an operation that delivers around 750kg of crisps every hour, typically working 16 hours a day although this can increase to 24 hours during peak demand.
“We have been delighted with the performance of the Ishida iTPS in terms of its accuracy, flexibility and reliability,” confirms George Taylor.
“We had used Ishida weighers as part of our potato packing business so we knew about the quality and reliability of the company’s equipment. What was particularly appealing about the iTPS was that it offered us a complete integrated weighing and bagging solution specifically developed for our type of operation.”
Mackie’s Crisps began manufacturing in 2009 as a joint venture between Perthshire potato farmers, the Taylor family, and Mackie’s of Scotland, renowned for its luxury ice cream. Since then, Mackie’s Crisps has become established as a leading brand in Scotland and has also achieved national listings in the UK as well as success in several overseas markets including Canada, France, Singapore and China.
As well as traditional varieties such as Sea Salt, and Mature Cheddar and Onion, Mackie’s offers several original specialities including Haggis and Cracked Black Pepper and Scotch Bonnet Chilli Pepper.