Neil Giles of Mettler-Toledo takes a look at some of the challenges facing companies in the food sector with respect to product inspection.
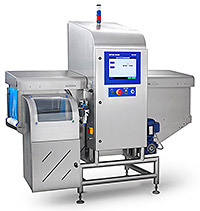
THE scrutiny that multinational organisations (MNOs) manufacturing food and pharmaceuticals are under to produce safe and high quality products is intense and growing more so.
Brand owners face expensive and damaging product recalls at the behest of state organisations, such as the UK’s Food Standards Agency (FSA) and the US Food and Drug Administration (FDA), if their products are found to be contaminated with foreign bodies, such as glass or metal fragments.
The FDA lists some two dozen recalls on its website for the month of December 2012 alone, while in the UK in the same period the FSA issued a product withdrawal notice for certain batches of cheese from three major supermarket chains due to the risk of metal fragments in the products.
Globalisation of food supply chains is increasing awareness of food safety across the board. Safeguarding public wellbeing and peace of mind presents a great challenge for food and pharmaceutical manufacturers, to which can be added the need to enhance supply chain efficiency. They have also to take into consideration the range of global and local food safety standards with which manufacturers must comply to retain access to markets. And then there is the growing importance of carbon footprint reduction and price pressures on raw ingredients to consider too. Product inspection technology is therefore of critical importance to maintain manufacturers’ competitiveness.
NAVIGATING THE SUPPLY CHAIN
Food and pharmaceutical manufacturing supply chains are becoming more complex, with raw ingredients being increasingly sourced from one part of the world, processed into a final product in a second region, before being exported to a third. This globalisation means that MNOs must comply with more and more regional regulation, particularly regarding the elimination of physical contamination from the supply chain through the use of inspection technology. They also must adhere to international supply chain standards and guidelines set down by individual retailers such as WalMart, Tesco and Marks & Spencer. The balancing act for MNOs is therefore to have a global presence, while retaining the ability to act locally to meet regional safety requirements.
This situation is not expected to become any easier in the near future. Indeed, more countries are expected to introduce regulations governing the manufacture of foods, requiring the use of precision metal detection and x-ray inspection systems capable of identifying foreign bodies in food and pharmaceutical products and removing rejected packs from the processing line. There is also a trend towards applying stricter guidelines inspired by those in effect in the pharmaceutical industry to food production lines. This is particularly true in the area of nutraceuticals – foods enriched with nutrients and vitamins – where traceability of products from the raw ingredient to the store shelf is an area of special concern for standards developers. Standards regarding ingredient declaration and labelling on packaging have become especially rigorous, leading manufacturers to invest in vision inspection systems to automate the label inspection process.
The 2011 US Food Safety Modernisation Act includes a number of clauses that previously only applied to standards for the pharmaceutical industry, such as the requirement for food manufacturers to adopt “track and trace” technology. In Europe, the General Food Law contains provisions for traceability, covering all food products and animal feed. China’s State Food and Drug Administration (SFDA) has introduced legislation making serialisation compulsory for both food and pharmaceutical products.
The Global Food Safety Initiative (GFSI) has had an important role to play in harmonising the many different regional standards for food safety, helping to increase the transparency and efficiency of the global food manufacturing supply chain, reducing costs and providing assurance of safe food for consumers. A number of retailers and governments have looked to the GFSI quality standards when developing their own guidelines and it will become increasingly important for manufacturers to be certified to GFSI-approved standards if they want to work with multinational food brand owners and supply major retail chains.
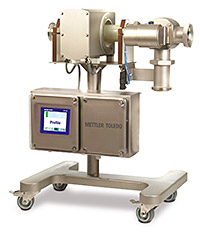
STREAMLINING PRODUCTION
In such an environment, strict control over production to minimise the risks of physical contamination becomes ever-more important. Added to this, the rising costs of raw ingredients used in food production and increasing labour costs help to bring the whole area of cost efficiency under the microscope. In response, they are searching for solutions, such as checkweighers or x-ray inspection systems, to monitor quality parameters such as fill-level, shape and size to reduce wasteful product underfill and overfill.
There are pressing economic needs behind the drive for greater manufacturing efficiency. Uptime of production lines is critical in meeting customer demands, and equipment needs to be fast, reliable, and easy to set up and changeover between jobs. Under the glare of scrutiny from agencies such as the FDA and FSA, food and pharmaceutical manufacturers also need data at their fingertips, providing an audit trail which proves that due diligence has been exercised throughout.
INSPECTION ADVANCES
Advances in product inspection technology include things like automated data collection that enables manufacturers to demonstrate compliance with food regulations to protect themselves against contamination claims. Product inspection systems, such as x-ray inspection machines, are being developed to further reduce energy consumption, allowing manufacturers to shrink their carbon footprint and support sustainability efforts.
Virtually all food and pharmaceutical manufacturing lines have unique requirements, and so it is important to select the most suitable product inspection solutions for each individual line. The process to find the right technology really begins with a Hazard Analysis and Critical Control Points (HACCP) audit on the food production line. This is a legal requirement in the EU and US, and is increasingly important in Asia. It will establish the most likely points of contamination on a production line. Where a risk is identified, a Critical Control Point (CCP) should be established immediately after the point where contamination could occur.
The HACCP audit also identifies the most likely forms of contamination at each CCP, such as metal or glass shards, stone or bone fragments, through the investigation of the origin of raw ingredients, the manufacturing process, and the packaging format. Product inspection systems can then be located at the point where they will be most effective, limiting the risk of foreign body contamination. The choice of technology then depends on the nature of the contaminant threat, and the specific location of the equipment is “validated and justified” by following the simple steps of the HACCP audit.
However, the installation of a product inspection machine does not automatically guarantee compliance with food safety guidelines. The equipment must be maintained correctly to ensure that it continues to perform with optimum detection sensitivity. The GFSI-approved British Retail Consortium (BRC) Global Standards, in effect in the UK and Scandinavia and recognised in many other territories, call for food manufacturers to put in place a maintenance schedule to monitor the performance of each foreign body detection machine. Manufacturers should also test inspection systems regularly using certified test samples. In the unlikely event of a failed test, all products manufactured since the last successful test should be quarantined for re-inspection. A good equipment partner can assist MNOs with all of these necessities, carrying out such line audits and providing comprehensive documentation systems that demonstrate due diligence and transparency.
Multinational food and pharmaceutical manufacturers face stiff challenges in respect of the weight of global awareness of food and drugs safety. Their production practices are under the microscopes of agencies such as the FDA and FSA as never before. Operating on a global basis and managing complex supply chains, MNOs must ensure compliance with each standard relevant in the region they are working in.