Ink migration continues to be a major concern with food packaging. Packaging Scotland looks at progress towards solving this problem, from new varieties of low migration ink to new paper grades incorporating protective barriers.
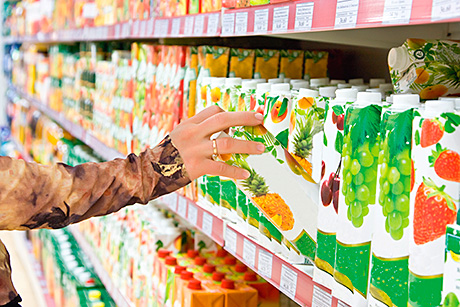
AN obvious downside to the more attractive, colourful, nuanced graphics that now adorn packaged products is the potential toxicity from all the chemicals that allow these fancy designs.
Ink migration is a serious concern in the packaging arena, not only from the inks used to design a package or label, but – in the case of packaging where there is a high level of recycled content (up to 96% with the white-lined chipboard consumers commonly see in primary packaging), from the residual inks left over from the material’s original purpose.
With aspects of packaging where there is a high level of recycled material present, there is always the need for greater attention to possible contaminants, especially when packaging food. A major component of the recycled material used for packaging is newspapers. Many of the printing inks used here contain mineral oil, which can remain in the fibres even after recycling. If these substrates are used for food packaging applications, the mineral oil components can migrate from the cardboard into the foodstuffs, even when food is protected by an inner bag.
Mineral oil barriers
An apparent breakthrough of recent months is the introduction of new mineral oil barrier (MOB) paper grades, brought to market through a partnership between Sappi, BASF and the testing Lab Eurofins. The new paper grades, MOB Kraft and MOB Gravure, are for inner bags and gravure printed primary packaging, respectively. The latter includes things like pouches, sachets, bags and wrappers. These promise to allow the use of a high level of recycled material in packaging, while eliminating the risk of potential contaminant migration.
MOB Kraft, for inner bags, combines Machine Glazed Bleached Kraft (MGBK) paper with the MOB barrier on the reverse side. MOB Gravure incorporates a blade coating on the top side, for gravure printability, and a MOB coating on the reverse, to protect the packaged product. Both have been shown to provide an effective barrier against the migration of MOSH (Mineral Oil Saturated Hydrocarbon) and MOAH (Mineral Oil Aromatic Hydrocarbon), substances suspected of being carcinogenic.
One of the challenges in its development, says BASF and Sappi, has been the realisation of a homogeneous coating layer to cover the pre-coated paper substrate 100%. “Small defects in the coating layer have an immediate impact on the quality of the barrier function. This requires first of all an extremely smooth and low porous base paper covered with a low porous and good covering pre-coat,” according to Jos Lycops, Senior Product Specialist, Sappi Central R&D. “Another challenge was to find an operating window on the coating machine to apply the barrier layer without blocking on the reel,“ he added.
The first customer request for the new MOB paper has been for dry food product pouches, to replace the currently used PVDC-coated variant, a material both expensive and containing chlorine chemistry. A spokesperson said: “Other brand owners in the food product arena have also shown a very high level of interest in our MOB paper development project. We anticipate that there will be good uptake on these grades as they are increasingly made available to the marketplace.”
The Sappi MOB Kraft and MOB Gravure grades are aimed at the sugar, chocolate and confectionery, coffee and tea, crisps, snacks and nuts, dried and dehydrated foods and frozen food and ice cream markets.
Developing low toxicity inks
But quite apart from the issue of residual ink remnants in recycled paper or card, there is the simple fact that many of the inks used in packaging bring with them an increased risk of mineral oil contamination.
Inkjet printing, especially UV inkjet printing, is becoming an increasingly popular print technique in the food packaging arena, given its ability to print on a wide variety of substrates and the relatively high throughput speed it can achieve.
In the past, the inks used with these printers were a particular concern from a migration point of view, given the presence of chemicals, especially photoinitiators, that presented strong concerns with respect to food safety.
While many printing technologies use physical barriers, primers and in-line laminates to prevent the migration of chemicals out of the printed layer of the packaging, these methods would tend to severely limit the advantages of using inket and UV inkjet printing.
The quest has therefore been underway to develop appropriate low migration inks for UV printing. These inks are designed to ensure that migration from the resultant printing ink film will be within accepted migration limits, provided that the packaging structure is suitable, and the packaging ink is applied under Good Manufacturing Practices in accordance with guidance given by the ink supplier for the intended application
A breakthrough five-colour UV inkjet ink was unveiled at the labelexpo exhibition in September, the fruit of a joint development effort between Sunjet and printing press maker Durst.
It can be used on a wide range of media such as PP and PE in the label sector, foil for food and pharmaceutical applications, and heat sensitive films for shrink sleeves, including an opaque white allowing for the use of clear substrates.
At labelexpo the ink was demonstrated working on Durst’s Tau 330 UV ink press, which is now being made available in a low-migration UV ink version.
Industry cooperation
Printing inks intended for graphics and general packaging are obviously not designed to come into direct contact with food. And the effort to ensure safety here requires ongoing cooperation throughout the supply chain, says Tony Mash of the British Coatings Federation. EuPIA member companies have signed Compliance Commitments related to the manufacture and supply of food packaging inks while the BCF has provided a lot of information about this on its website at www.coatings.org.uk.
Sunjet’s ink complies with all the EUPIA guidelines and the Swiss Ordnance on Materials & Article legislation. It also does not use materials prohibited under the Nestle Packaging Inks Specification.