While the plastics industry traditionally gave little thought to recycling, by 1991 the issue had moved into the spotlight with the emergence of new regulations in Germany. This article offers a German perspective on some of the progress being made with plastic packaging recycling in Europe
SINCE the early 1990s many countries in Europe have developed highly successful strategies for collection and recovery. According to surveys by Plastics Europe about 47 million tonnes of plastics were consumed in the 27 countries of the EU plus Switzerland and Norway in 2011 (with a 40:60 split between non-durable and durable applications respectively). In the same year, some 25 million tonnes of waste plastics were collected, 40% going to landfill and 60% being recovered.
The waste from collection systems for used packages accounted for over 60% of this, followed by products from the construction, automotive and electronics sectors. Exemplary collections systems are in place in nine European countries: Switzerland, Germany, Austria, Belgium, Sweden, Denmark, Norway, the Netherlands and Luxemburg (listed in descending order) with collection rates ranging from 99 to 92%. At the same time, six of these countries have the highest recycling rates in Europe: Norway, Sweden, Germany, the Netherlands, Belgium and Austria. The remaining collected wastes are recovered to generate energy by incineration.
PET bottles are also amenable to single-grade sorted-waste collection and processing. The spectrum of products made from them range from fibres and films to new bottles.
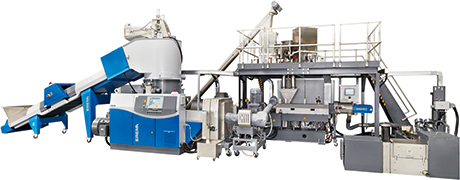
Problems facing recycling
Plastics items of different materials that cannot be sensibly separated constitute a further obstacle to recycling – as do products whose residues are difficult to entirely remove. Problems are also created by post-consumer film wastes, as they manifest a very poor ratio of surface area to contamination and therefore require laborious treatment. According to Michael Scriba, md of plastics processor MTM Plastics in Niedergebra, there are indeed successful recovery specialists, but as yet no established sales markets with a Europe-wide reach. Further challenges are posed by non-beverage bottles made of PET in a huge variety of types, which also have limited recoverability. Much the same applies to plastics from car and electronics residuals.
For such challenges, processors and machine manufacturers are called upon to come up with appropriate solutions. For example, one solution for post-consumer film wastes from DSD collections has been recently supplied by Herbold Meckesheim GmbH in Meckesheim to the waste disposal company WRZ-Hörger GmbH & Co. KG in Sontheim. The turnkey plant, consisting of a separation device for removing extraneous substances, a wet shredding step and a Plastcompactor, converts 7,000 tonnes of wastes per year into free-flowing agglomerates with a high bulk density that can be used for the production of injection mouldings. Especially for mixed fractions, Erema has teamed up with Coperion GmbH & Co. KG in Stuttgart to develop their Corema, a combined recycling and compounding line. Characteristic of this unit is its suitability for a wide range of materials. According to Erema md Manfred Hackl, this is an ideal machine for processing mixtures of materials obtainable at low cost and for converting PP non-woven wastes into a compound with 20% talcum and for processing PET/PE mixtures with additives.
Another special solution is the MRS extrusion system supplied by Gneuss to K2 Polymers in the UK for the processing of polyamide 11 regrind. The feedstock comes from deep-sea oil pipes recovered from a depleted oilfield and brought ashore. After decades of service, these pipes are highly contaminated with oil. The Multi Rotation System (MRS) extruder manages to decontaminate and reprocess the high-grade plastics waste in a single step and without chemical washing.
Although many processes have already become established, recycling still has plenty of potential for improvement.